39 Coring Equipment and Tools
CORING: THE SCIENCE OF DRILLING FOR OCEAN FLOOR SAMPLES
At the heart of core retrieval on a scientific ocean expedition is the drilling process. This is especially true for JOIDES Resolution which reached impressive depths. The ship was capable of drilling in water depths of up to 8,235 meters and could suspend up to 9,150 meters of pipe to the seafloor.
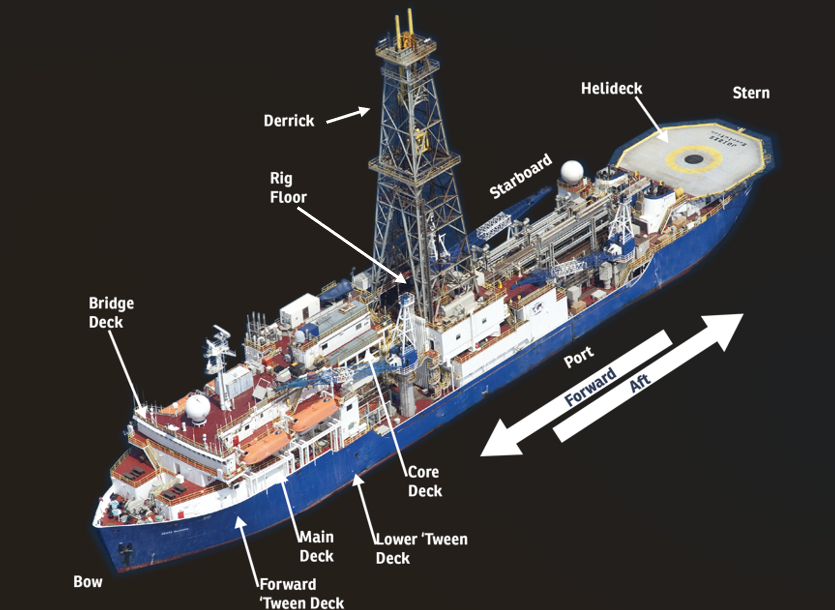
KEY DRILLING EQUIPMENT: THE BIG PIECES
Drilling operations on the JOIDES Resolution relied on several large pieces of equipment to safely and efficiently recover sub-seafloor samples. The derrick, rising 60 meters above the water line, was the steel structure towering over the rig floor. The derrick supported the drill string, multiple 30 meter long stands of pipe and a bottom hole assembly (BHA) which contains the drill bit.
A stand is made of three nearly 10-meter-long pipes screwed into one another, each weighing nearly one ton. The number of stands would change, depending on the depth the drilling. The derrick also provided the necessary height for lifting and lowering drill pipes into the borehole. The pipe stabber grabbed a stand, resting horizontally in the aft of the ship and brought it to the rig floor where the elevator handler would turn it to the vertical position so it was ready for drilling.
In the drill shack, commonly known as the Dog House, drillers monitored and controlled drilling operations by use of brakes and winches, lifting devices that carry the entire weight of the drill string. Another essential tool was the Iron Roughneck, often called the boot on the ship. This hydraulic device applied enough torque to tightly screw or unscrew the pipes together.
Together, these components provided the essential strength and power to the drilling operation, ensuring precision and safety throughout the core retrieval process. The following interactive graphic shows this equipment on JOIDES Resolution’s rig floor.
In the above image, one can see different areas of the rig floor with blue plus signs. Click on the signs to learn more about those pieces of equipment.
What is the drill string?
The deepest hole ever drilled on a single JOIDES Resolution expedition reached an incredible 1,806 meters (1.12 miles)* beneath the seafloor. To even start coring, the JR plumbed water depths up to 5,012 meters (3.11 miles)*. Reaching so far down requires an immense lengths of total drill pipe. The drill pipe was stored near the aft of the ship as stands on the pipe racker. Take a look at the numbers behind the JR’s stored pipe supply.
*Source: https://iodp.tamu.edu/publicinfo/ship_stats.html
Miles of Pipe for Miles of Discovery: JR’s Racker Statistics
The JR pipe racker could fit two sizes of drill pipe in the racker system, and there were three pipe rackers.
- One racker was dedicated to 5-1/2-inch drill pipe and could hold 98 stands (294 joints) of 5-1/2-inch drill pipe. Each joint was about 9.6 meters long, each stand about 28.8 meters. Therefore, the 5-1/2 inch racker could hold up to 2822 meters (1.75 miles) of pipe.
- The two rackers dedicated to holding 5-inch drill pipe could hold 126 stands (378 joints at 9.6 meters per joint) which was approximately 3628 meters ( 2.25 miles) per racker for 7256 meters (4.5 miles) total 5 inch drill pipe.
JOIDES Resolution normally had about 50 stands of 5-1/2-inch drill pipe in the racker (1440 meters/0.89 miles) and about 150 stands (4320 meters/ 2.68 miles) of 5-inch drill pipe total.
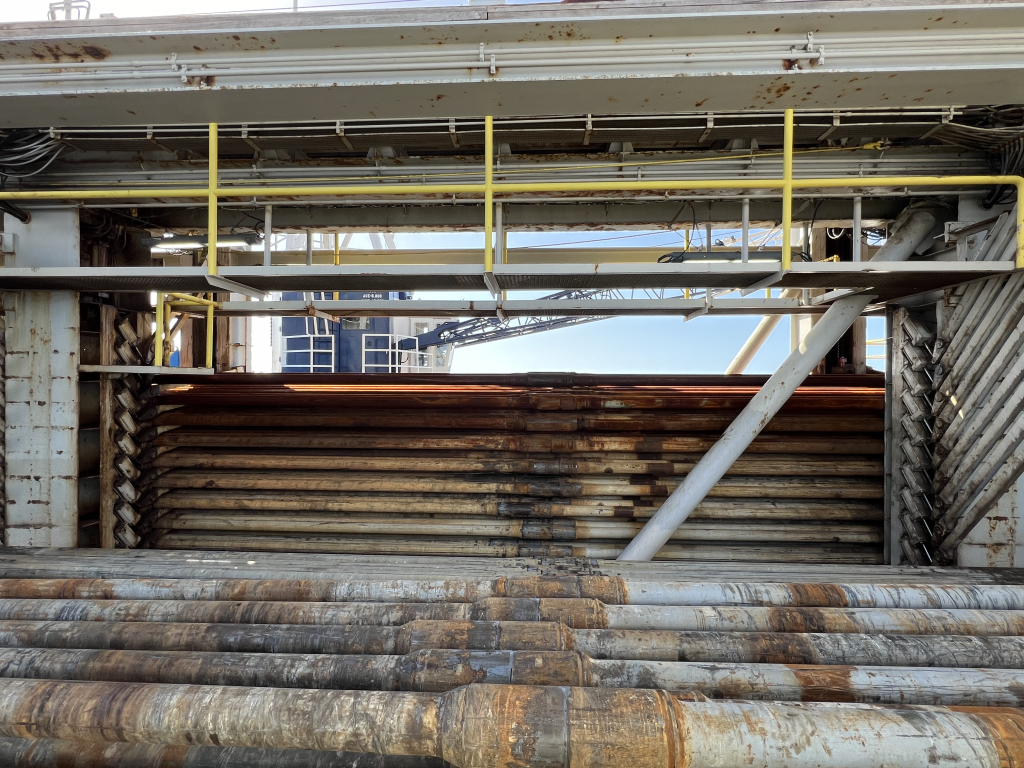
After individual stands were brought up to the rig floor by a vertical conveyor belt, the pipe would go through the pipe stabber. This process aligned the end of the stand right in between the travel block bails (two long arms that hang down from the travel block). Once aligned, the elevator would be latched closed around the pipe so that the travel block could pull the pipe stand upward from a horizontal position to a vertical position. The pipe stand would then be completely vertical in the derrick above the rig floor.
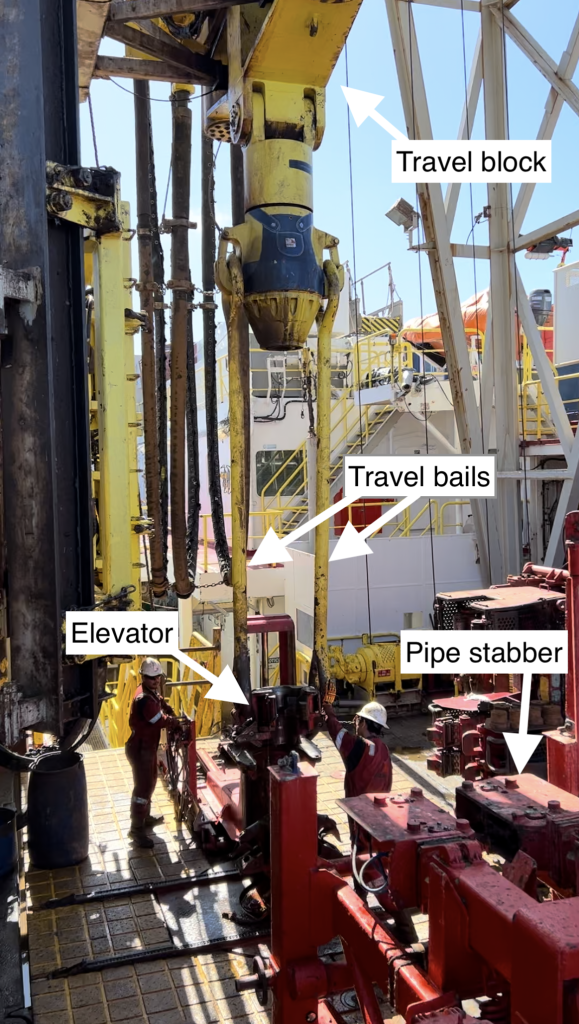
Getting Ready To Drill: Tripping Pipe and The Bottom Hole Assembly (BHA)
Before the ship even arrived at a drilling site, the rig crew was tripping pipe, the jargon used on the ship when referring to building or dismantling the drill string. The drill string was made up of multiple 30-meter long stands of pipe and a Bottom Hole Assembly (BHA) which contained the drill bit. Regardless of depth, constructing the full drill string took approximately 12 hours, and dismantling it required the same amount of time.
Exploring what it means to “trip pipe”
The jargon used on the ship when referring to building or dismantling the drill string was called tripping pipe. Crew members wrote and recorded a song about this process.
During JOIDES Resolution operations, the drill string had to strike a delicate balance—remaining rigid in the borehole while staying flexible in the water column to allow for changing sea conditions. The (BHA) was the most rigid part of the drill string, ensuring stability as it maintained continuous contact with the seafloor. This rigidity was crucial for effectively cutting into the sediment and rock while preventing unnecessary movement within the borehole. Meanwhile, the upper portions of the drill string remained flexible, allowing the system to adapt to ocean swells and shifting currents without disrupting drilling operations.
The (BHA) varied depending on the type of coring being conducted, but it typically included key components that provided the rigidity and necessary weight for greater drilling force. Drill collars were used to add weight to the drill bit, helping it penetrate the seafloor more effectively. Drill subs served as transition pieces, allowing different components of the BHA and drill string to connect seamlessly. At the cutting edge of the operation was the core bit and drill bit, which was specifically selected based on the seafloor formation to ensure efficient and successful coring. Depending on how long coring would take and if one encountered hard rock, a borehole would utilize more than one drill bit, because time to failure was about 60 hours of use for hard rock drilling. The JR would travel with multiple drill bits at all times.
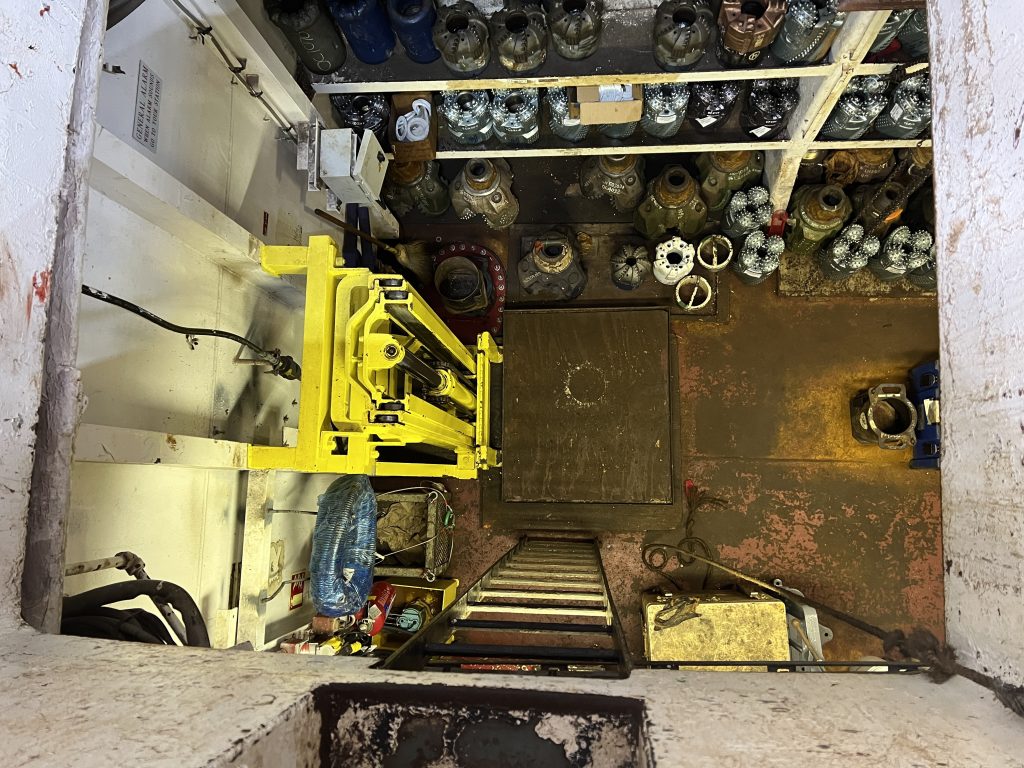
Drill Bit vs. Cutting Shoe: How They Work Together
Another part of the rigid coring apparatus was the cutting shoe. When discussing coring, the terms drill bit and cutting shoe often come up together because they function as a team. The drill bit cuts the borehole, while the cutting shoe is responsible for cutting the core itself. Coring drill bits are designed with a circular opening in the center, allowing for the retrieval of the core sample.
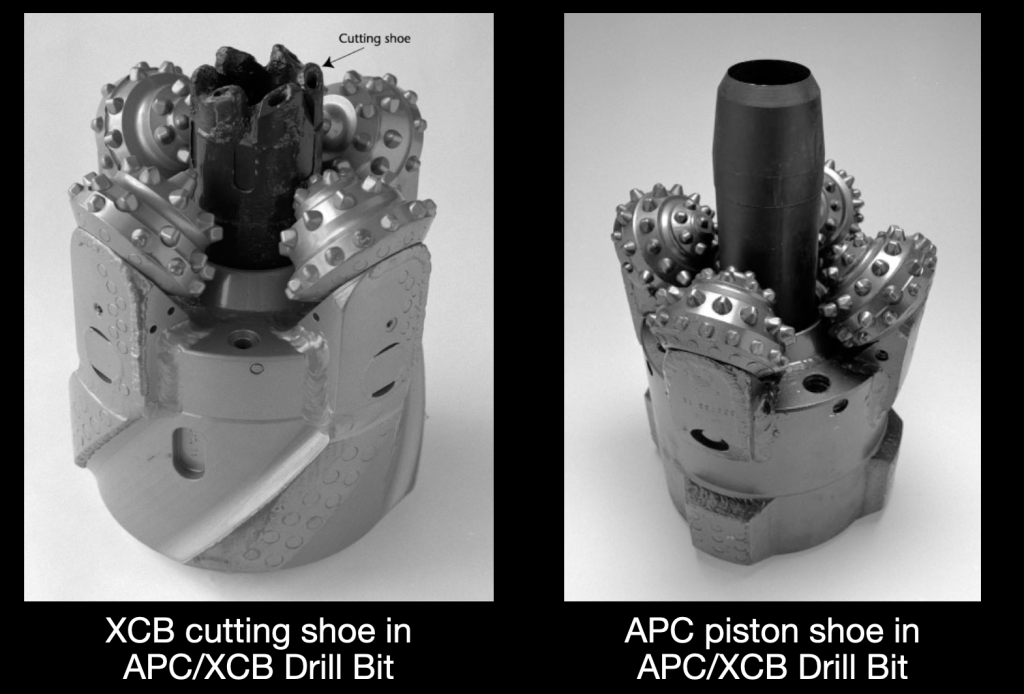
For sedimentary coring (APC/XCB), the drill bit has a wide circular opening to accommodate the APC cutting shoe, which must extend beyond the drill bit to punch through the sediment. This is a fast and efficient process since the formation is soft, meaning the drill bit’s rotary cones do not need to grind the material. In XCB coring, the cutting shoe sits just ahead of the drill bit, cutting harder sediments while the drill bit rotary cones begin to engage under compression, slowing the coring process compared to APC.
For RCB coring, used in hard rock drilling, the drill bit has a narrow circular opening, positioning the cutting shoe just behind it. In this case, the drill bit does most of the cutting for both the borehole and the core, as the harder formations require more force and durability.
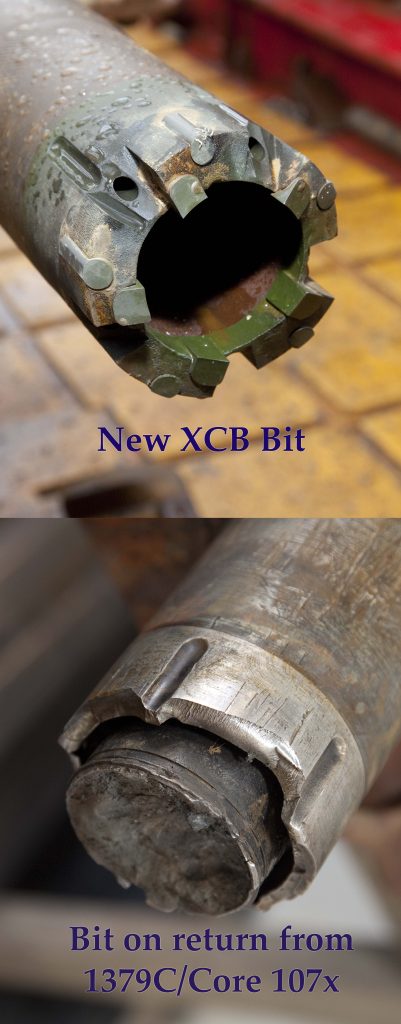
Selecting the Right Drill Bits and Cutting Shoes
Before each expedition, the JOIDES Resolution’s Ship Operations team determined which drill bits, cutting shoes, and core barrels would be used at each drilling location. This planning allowed the rig crew to pre-build the drill string before even reaching the site. These decisions were based on seismic survey data collected during pre-expedition research cruises, ensuring the equipment matched the expected seafloor conditions.
In the following video, one can see the rig floor crew assembly the BHA as part of the drill string using the machinery and instruments listed above. The videos demonstrates how the rig floor crew utilized all the components mentioned earlier to build the drill string, also called tripping pipe. The first scene on the rig floor was the rig crew pulling up the first BHA stand that was already connected to the drill bit. Towards 1:29 minutes, one sees the rig floor crew handle the travel bails, elevator, and elevator handler to connect a new stand to the already deployed one. The rest of the video transitions into showing the rest of the drill string being built and put through a hole in the rig floor that opened up to the ocean.
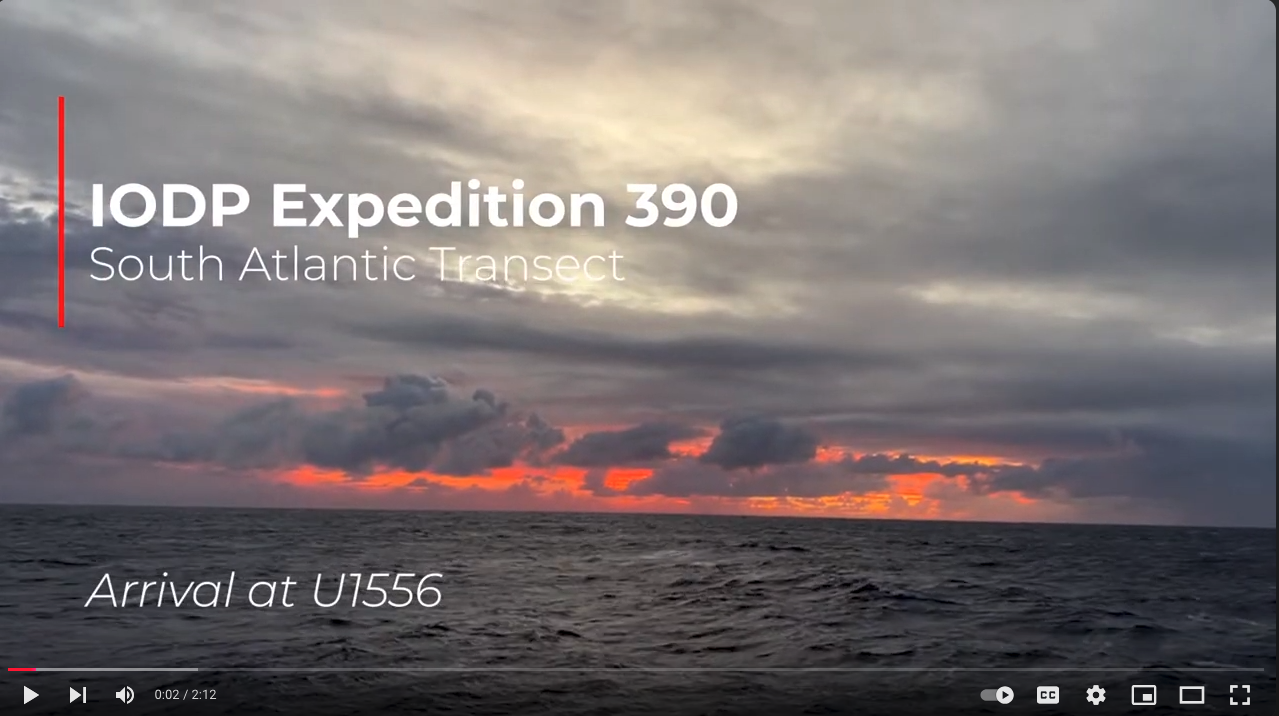
Drilling Soft, Drilling Hard, Drilling Harder
DRILLING IN SOFT FORMATION: Generally for soft sediment seafloor formations the Advanced Piston Coring (APC) cutting shoe was ideal for core collection as it punches through ahead of the drill string instead of rotating down. The action of punching through reduces the amount of disturbance the drilling action has on the soft sediment core. When there is less disturbance, it makes for smoother data collection for the sedimentologists and paleomagnetists.
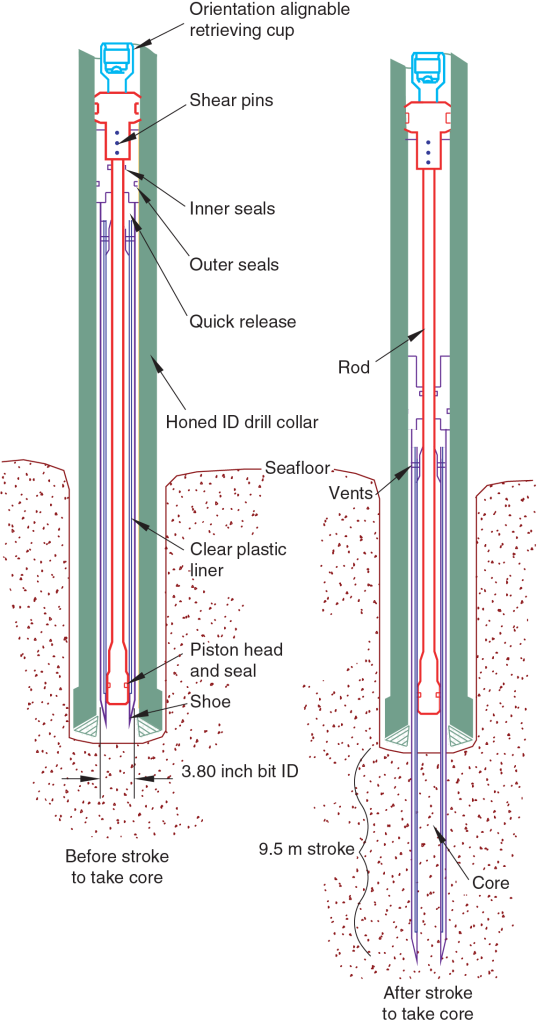
One fact to note about APC coring on the JR is that it was much faster than other coring, so much so that the rig crew could deliver a new 9.5 meter core to the rig floor every 20-50 minutes (depending on water depth). This short time frame between cores was extremely strenuous for technicians and scientists because the core flow (the path a core took to move through all the instruments in the lab) itself took a few hours longer than that.
The below video provides a close up visual of the rig floor crew bringing up one core barrel, and switching it out to send down a new core barrel to continue coring. Plus, one can see the iron roughneck used to close the two pipe stands together.
DRILLING IN HARD FORMATION: The Extended Core Barrel (XCB) cutting shoe was used in cases of harder or tougher sediment, or the interface between soft sediment and basement was expected to be reached. The time to deliver a new core utilizing XCB took a little longer than APC, which meant a wait of a few hours in-between two different cores. Fortunately, the XCB cutting shoe and the APC cutting shoe used the same BHA, meaning the rig crew only needed to change out the type of cutting shoe rather than the entire drill bit. To be more specific, when the rig crew would change the cutting shoe, they would screw on the cutting shoe to the next core barrel, which moved freely through the drill string on a smaller winch line. If they had to change the entire drill bit (at the bottom of the drill string), they would be required to undo the entirety of the drill string and rebuild the string to attach a new drill bit using up 24 hours of operational time.
DRILLING IN HARDER FORMATION: Rock is, as expected, a hard formation to drill into for a core and would take the longest to drill through (>5 hours). The cutting shoe used for rocky formations was the Rotary Core Barrel (RCB) and had a completely different BHA than the XCB or APC. A distinct feature of RCB coring was that the rotary cones on the drill bit turned under the compression of the drill string, and that action that was utilized to grind the borehole and core. The ship achieved compression on the cones by adding weight to the drill string via number of pipe stands and what kind of BHA was used. Through careful monitoring of how much weight was on the drill bit, the driller could determine how effective drilling was going, how fast or slow to drill and more. With no weight on the drill bit, the cones themselves would not turn. Essentially, not enough weight lead to no coring, and too much weight grinds up both the borehole and the core together.
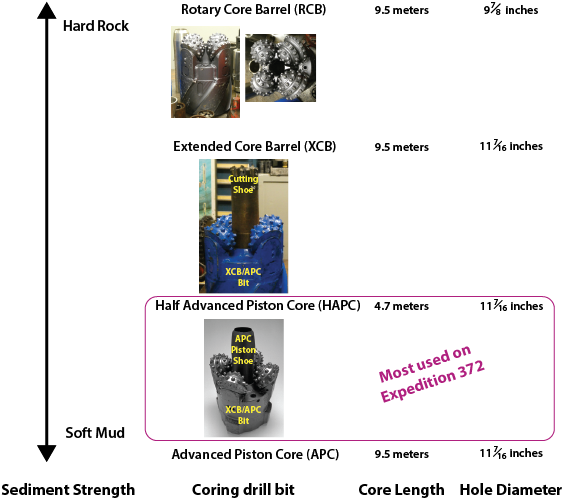
The above diagram mentions the half advanced piston core, which is still a type of APC drilling. It was used when there were concerns about recovery. Recovery references how much of the core was being sampled and brought back up to the ship. Generally, APC had near 100% to more than 100% recovery, while hard rock drilling recovery could vary wildly. However, if the soft formation was too soft, the water that was pumped into the borehole to cool down the drill bit and cutting shoes could lead to washing away the soft formation before being cored. To avoid or mitigate such instances, half advanced piston coring was a chosen strategy. The equipment used for drilling HAPC mostly stayed the same compared to APC, except for the core barrel, which was a shorter length.
Summary
The main points of the coring equipment used included:
- The drill string is used to connect the ship to the seafloor during coring processes
- The BHA is the most rigid part of the drill string and is the part of the drill string that is attached to the drill bit
- It takes 12 hours to assemble the drill string, and 12 hours to disassemble it
- There are different drill bits used for different seafloor formations
- There are different cutting shoes used for different seafloor formations (APC, HAPC, XCB, RCB)
- There are drill bits that are paired with certain cutting shoes
- The cutting shoe is attached to the core barrel that drops from the ship through the drill string into the seafloor, and the core barrel with the core is brought back up to the ship once a specific distance is achieved. The drill string does not come up with the core.