2 The Lifecycle of a Building Project
Learning Objectives
After reading this chapter, you should be able to:
- Define the four primary phases of the lifecycle of a building project
- Describe various unique aspects of a building project in relation to the manufacturing industry
- Define the total cost of ownership, and the impact of decision timing on overall lifecycle cost
The Construction Industry is composed of projects. A core skill set for everyone within the industry is the ability to manage projects, whether you work in project development, architectural design, engineering design, construction or facilities management. Project Management is ‘the application of knowledge, skills, tools, and techniques to project activities to meeting project requirements’ (PMBOK Guide 2000). Projects are not unique to construction. For example, some other industries are also very project-focused, e.g., aircraft, computer software, shipbuilding, etc. The Project Management Body of Knowledge Guide (PMBOK) has been developed by the Project Management Institute (PMI) as a general set of knowledge for managing a project. The core management areas identified in PMBOK includes the following (from PMBOK Guide and the Construction Extension of the PMBOK Guide):
- Project Integration Management
- Project Scope Management
- Project Time Management
- Project Cost Management
- Project Quality Management
- Project Resource Management, including Human Resources (Construction Extension highlights additional resources beyond the standard Human Resources in PMBOK)
- Project Communications Management
- Project Risk Management
- Project Procurement Management
- Project Health, Safety, Security, and Environmental Management (in Construction Extension, but should be in every project)
- Project Financial Management (in addition to cost) (in Construction Extension)
- Management of Claims in Construction (in Construction Extension)
The Process to Deliver a Facility
A building project is composed of processes. A process is ‘a series of actions bringing about a result’ (PMBOK). Each process is performed by a person or organization Generally, there are two broad categories of processes: project management processes and product-oriented processes (PMBOK).
A project proceeds through a lifecycle. A facility is planned, designed, constructed, and operated (see Figure 2-1). This lifecycle, and the importance of taking a lifecycle perspective on projects, has sometimes been referenced as a Cradle-To-Grave perspective. From a lifecycle perspective, all materials and systems should be evaluated relative to their value in supporting the lifecycle goals of a building or facility.
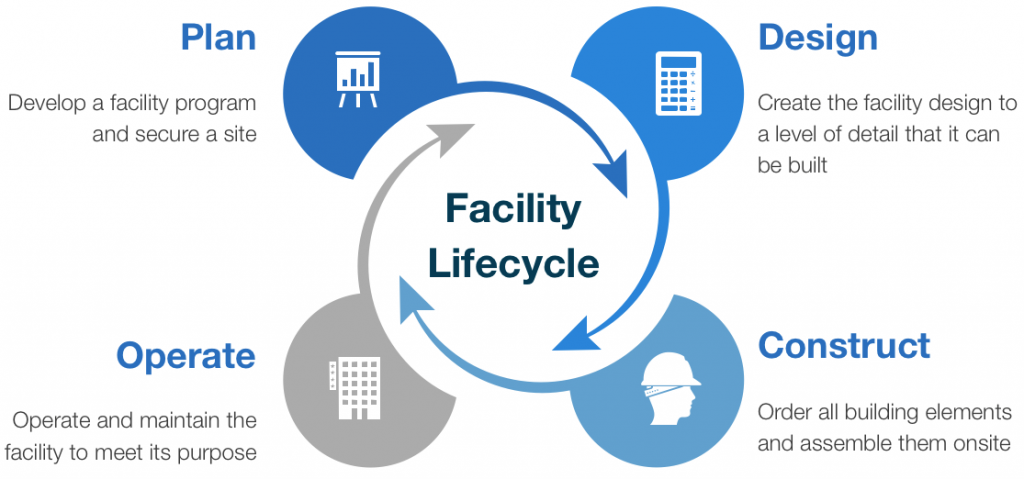
Some have expanded upon the concept of Cradle to Grave by considering the lifecycle as a continuous process and proposing a reference to Cradle to Cradle (C2C). C2C emphasizes the need to consider the reuse or recycling of products that are used within the delivery of a building.
Sanvido et al. (1990) developed a detailed process model to define the various tasks that need to be completed to deliver and operate a facility. The process model is titled the ‘Integrated Building Process Model’ (IBPM). This model is created using the IDEF0 process modeling approach. Each ‘process’ (a box) can be expanded into another more detailed process map showing additional detail. The Level 1 process map shows five main activities within the process:
1) Plan Facility
2) Design Facility
3) Construct Facility
4) Operate Facility
5) Manage Facility
Note that the Manage Facility process interacts with the remaining four project phases, so we will not consider this as a primary product-oriented process of the project lifecycle, but instead, a map that shows typical management tasks that need to be completed (a project management-oriented process). Also, note that IDEF0 process mapping does not necessarily indicate a linear sequence. Many of these processes can overlap, and they may not be in the specific order in which they will be performed. The Level 1 process map is included in detailed process maps are included in Figure 2-1. The more detailed process maps for each of the 5 phases are included in Figure 2-2 through 2-6 within the following sections describing each phase. If you wish to see detailed information about any process, you can reference the Integrated Building Process Model technical report.
Planning Phase
During the planning stage, the Owner of the facility will need to define their project needs, identify the general budget and schedule, and potentially identify a site for the building. The owner may employ the services of an architect, contract developer, or other professional to help them define their needs, and identify the resource requirements. The final outcome of the planning phase is a ‘Program’, or in some countries, a ‘Brief’, which clearly defines the owner’s needs and a plan to design and construct the facility. They will also need to identify, and sometimes purchase, a site for the facility.
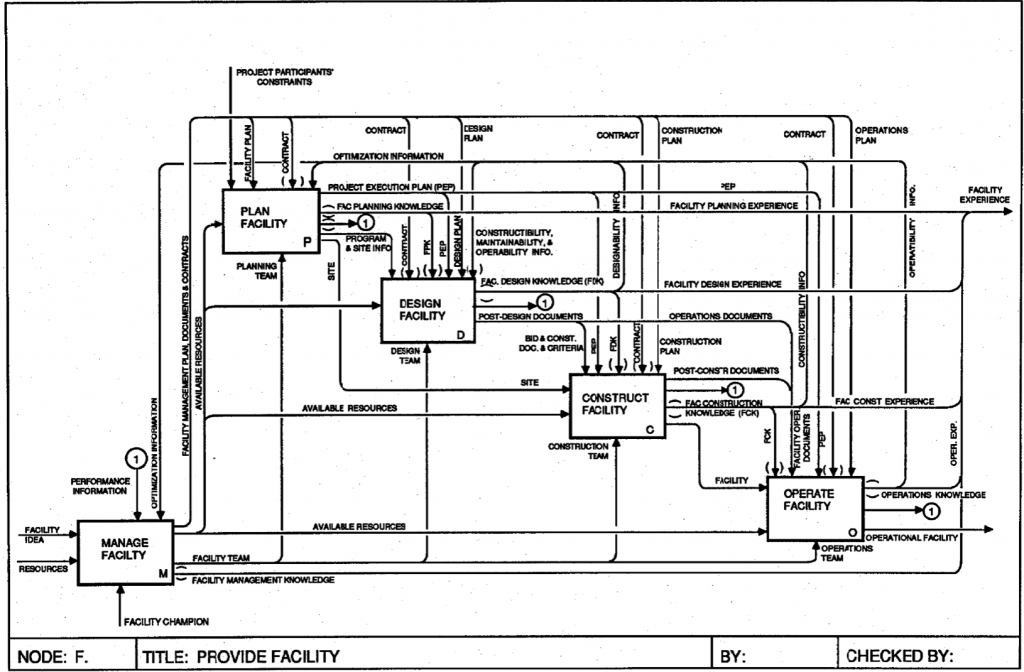
Design Phase
Within the design phase, a designer will interpret the needs of the owner into a design for the facility which is to a level of detail that it can be built. The design phase is frequently divided into three levels of design:
- Schematic Design (SD): Perform an evaluation of the owner’s needs, and develop an initial design concept. Typically, the industry has considered this level of design to be approximately 30% complete.
- Design Development (DD): Expand the initial concept to define the systems that will be used and general materials. Typically, this has been considered approximately 60% design completion.
- Construction Documents (CD): Finalize the design details to a level that they can be built. Complete all design specifications and construction drawings.
The full scope of these design tasks will typically be defined within the contract with the designer (or integrated team if using a more integrated delivery approach). To see the typical definitions of the scopes within these phases, you can view the typical Owner – Architect Agreement from the American Institute of Architects (AIA) within their AIA B101 document (see pages 6 – 8 of this online sample document for the definitions of each phase).
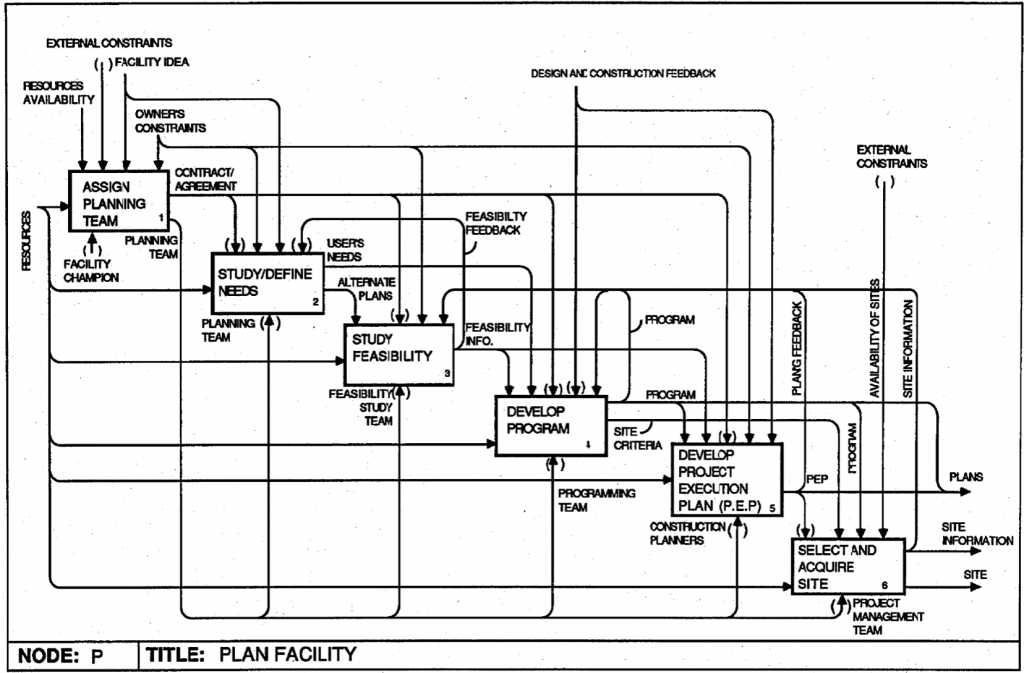
Construction Phase
Within the construction phase, a contractor will lead the assembly and construction of the facility. This will include the procurement of all the elements needed to build the facility, including arranging for the elements to be transported to the site. After arrival, the building component will be assembled on-site and tested to ensure the appropriate level of quality. The constructed facility will also require any inspections by governing authorities to ensure that it is safe to use for its intended purpose. For a building project, the primary construction phase typically ends when the contractor obtains a ‘Certificate of Occupancy’. The Certificate of Occupancy is issued by the local governing authority or code office, and it certifies that the building complies with the codes and requirements and that the owner can occupy the building.
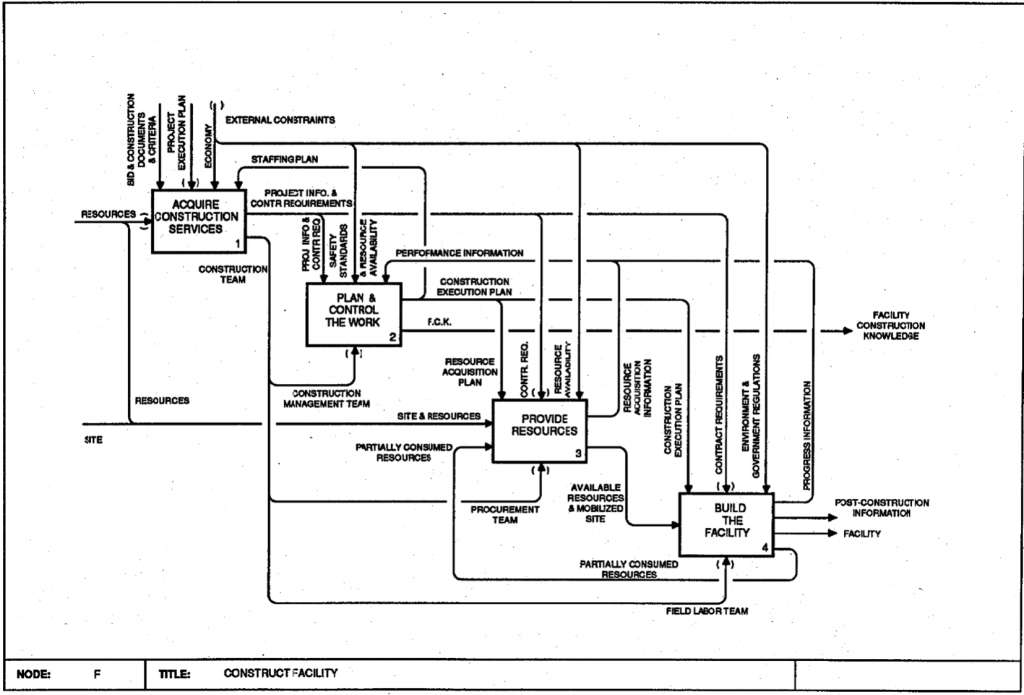
Operations & Maintenance Phase
The Operations & Maintenance (O&M) phase is typically the longest phase within the facility lifecycle. In this phase, the owner will use the facility for its intended purpose, and they will need to operate and maintain the functionality of the facility. In some research, up to 80% of the entire lifecycle cost of a facility is spent in the operations phase. Activities that occur within the phase include the maintenance of equipment, the replacement of materials and equipment that require replacement, and minor renovations to allow for revisions of facility use. This phase is also sometimes referred to as Facility Management (FM), and an owner may perform the facility management services within their own internal employees, or they may hire a 3rd party FM service provider.
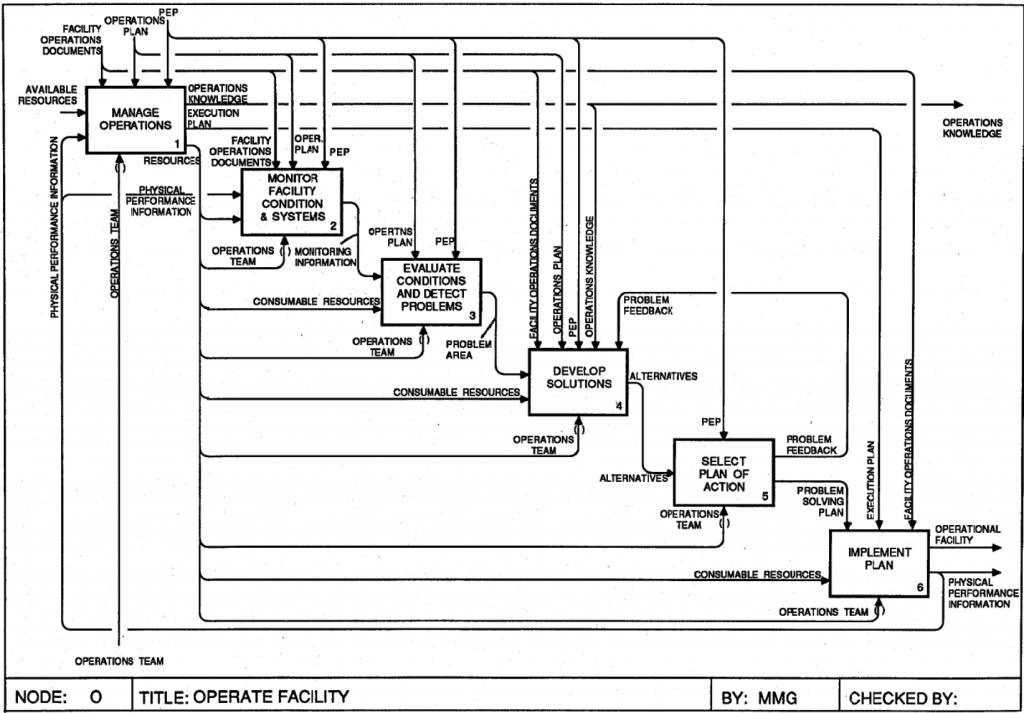
Manage Facility
In addition to the unique four phases, there is a need to coordinate and manage the process and resources throughout the lifecycle. These processes were defined within the IBPM within the Manage Facility process (see Figure 2-7). Note that this is NOT a phase of a project, but instead tasks that are performed throughout the lifecycle process.
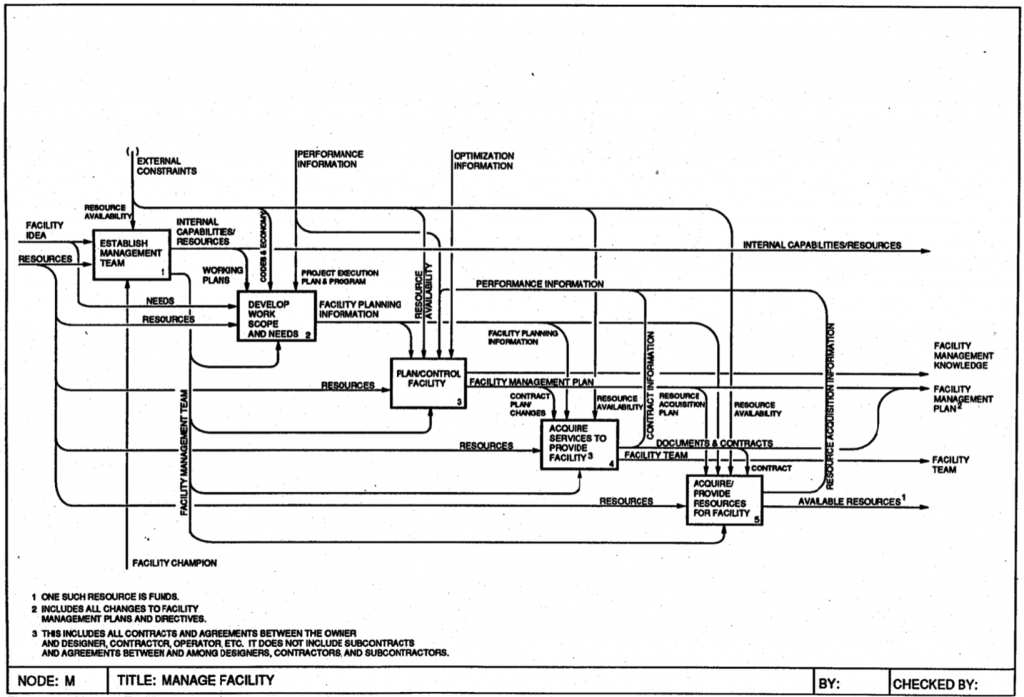
Unique Aspects of Construction
Projects and the structure of the industry have several unique characteristics that influence our management approaches. Several characteristics include:
- All projects are unique. Even if a project is a duplicate design of another project, the project will be located on a unique site, which includes unique constraints.
- Projects are performed outside, at least until an enclosure is developed. This is different from manufacturing which may occur within a controlled environment. Therefore, construction is influenced by the environmental conditions of the geographic location of the project.
- The Construction Industry has many companies. The AGC states that there are over 650,000 companies that employ workers within the construction industry. This is a very large number of firms, and some of these companies may only have one employee. But it is also important to note that the largest contractors are quite large, but it is still a fragmented industry with many companies.
- There are many organizations that work together to deliver a project. It is not uncommon to have more than 20 companies working on the construction of a project, with workers in the field, and there are many other companies involved in designing the facility, and supplying materials and equipment to the project.
- Design and Construction companies do not tend to perform much research and development. Due to the lower profit margins in the industry, and a shorter-term focus, most firms do not invest in research. There are certainly exceptions, but as a percentage, the industry has very low investments in R&D.
- The industry is impacted by geographic ties. Since buildings are constructed in many different locations, there are different code requirements in different locations and different companies with employees and experience in working in the local markets.
- The industry has a high rate of business failures. Due to a large number of smaller firms, it is not uncommon for businesses to fail.
- There is a low barrier to entering the construction market. In fact, it is quite easy for an individual to open a construction company. It may only require some simple paperwork, or they may need to apply for a contractor license.
- Organizations change from project to project. It is very rare to have the same organizations work together on multiple projects. This requires members in the industry to specialize in working with new team members since the mix of team members, including designers and contractors, will change on each project.
- Construction is a hybrid industry. Some tasks are service tasks, e.g., the design of a facility or managing the delivery of a facility. Other tasks are closer to manufacturing, with a focus on producing the facility. Examples of these tasks include building the structure, installing the mechanical/electrical/plumbing (MEP) equipment, or installing the facade. Therefore, the industry is a hybrid between a service and manufacturing industry.
Total Cost of Ownership
It is critical for the owner, and the entire project team, to view a project from a total cost of ownership (TCO) perspective, which considers the costs, along with overall environmental impact, of all phases of the project lifecycle. It is very important to note that the vast majority of the decisions that influence the lifecycle cost of a facility are made in the earliest phases of a project, e.g., planning and early design phases. This concept has been included in quite a few different diagrams. Figure 2-8 is a simple representation that shows the construction costs over time (dashed line) where the costs are low in the beginning, and accumulate over time. The ability to influence the cost is represented by the solid line which shows that it is much more difficult to influence costs as the project design and construction continue. For example, in the early stages of a project, it is much easier to alter a system to reduce costs, but after the design is developed and the materials are ordered, then it can be very difficult to reduce overall costs, even if it is a less expensive system, due to the costs of making the change. It is also interesting to consider the overall business and societal costs and impacts of a facility. Some have estimated (although not with much data) the overall impact of facilities on organizations and society, and they show that the societal impacts of facilities are significantly greater than the initial cost of design and construction (see Figure 2-9).
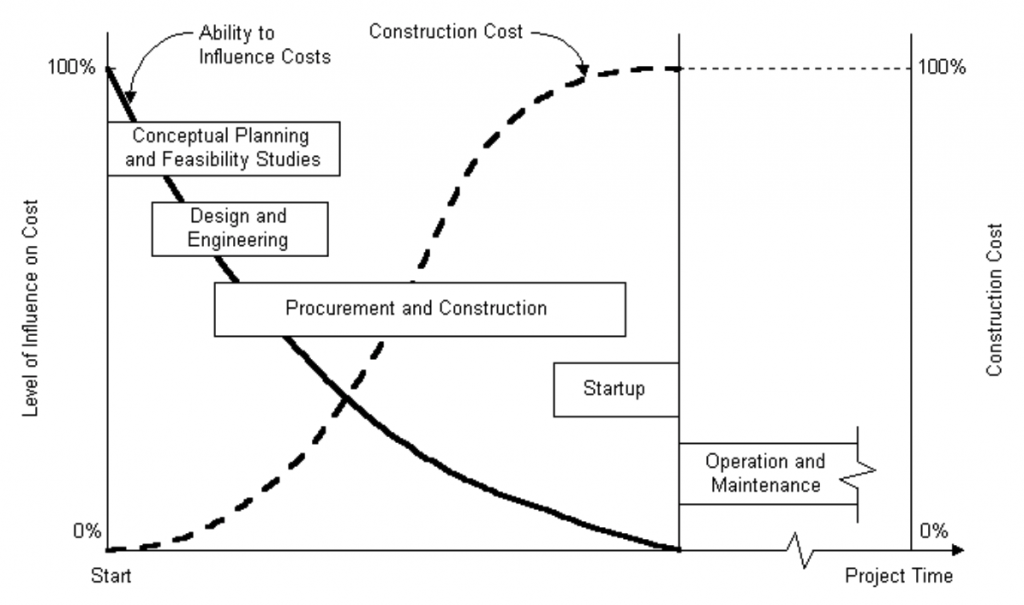
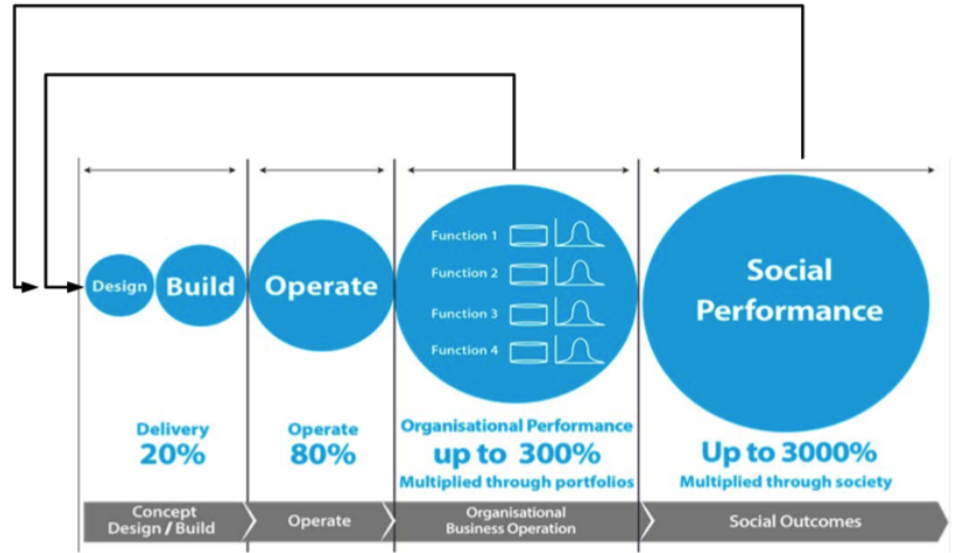
Chapter Review Questions