9 Unit Price Cost Estimating
Learning Objectives
After reading this chapter, you should be able to:
- Describe the benefits and limitations of the unit cost estimating approach
- Develop a unit cost estimate for a portion of a building project
- Identify the detailed cost components within a unit price estimate, and how these cost elements are calculated
As the detailed information is developed within the construction documents phase of a project, the project team can develop detailed cost estimates using the Unit Price estimating approach. The Unit Price estimating approach is focused on identifying a cost for the materials, equipment, and labor for each of the components within a building. This requires an estimator to perform a detailed takeoff of all scopes of work.
Unit Price Estimating with R.S. Means Data in the Gordian Guides
Unit Price estimates for commercial building projects are typically organized by the CSI MaterFormat categories (see Fig. 9-1 for CSI MasterFormat 2016 Version categories). The detailed CSI Materformat breakdown can be found at https://www.edmca.com/media/35207/masterformat-2016.pdf. In this class, we will use the RS Means data for identifying the cost for each of the items within the estimate, but it is important to realize that construction companies will frequently use their own historical cost information for estimating each item. To be successful at using their historical information, they need to make sure that they are accurately tracking their costs on projects, and placing them in a database that can be easily searched and retrieved.
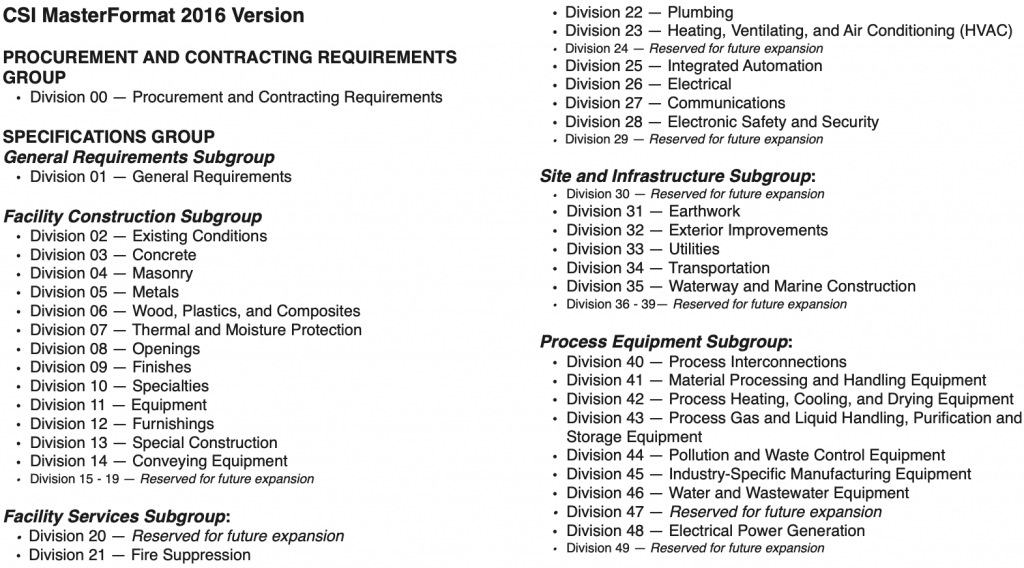
If you do not have your own historical cost database, then the next best approach is to use cost data contained within published cost guides. For our estimating exercises, we will be using the Gordian Construction Cost Estimating Guide with RS Means Data. Examples of the information published in this Guide are shown in Figures 2 and 3. To develop a cost estimate for an item, you should first identify the unit of measure for the item. Then, a detailed takeoff will be performed to identify the quantity of the item within the project. After performing the takeoff, the item can be estimated. You’ll notice that the Guide provides a summary for both ‘Bare Costs’ and ‘Total Including Overhead and Profit’. The bare costs can be used in an estimate where the estimator incorporates a separate, specific overhead estimate and actual projected profits.
After identifying and compiling quantity and cost data for each of the individual items, these items can be combined into the final estimate. An example of compiling the estimate is included in Figures 4 and 5.
Please reference the course slides to see additional details regarding the Unit Price estimating approach.
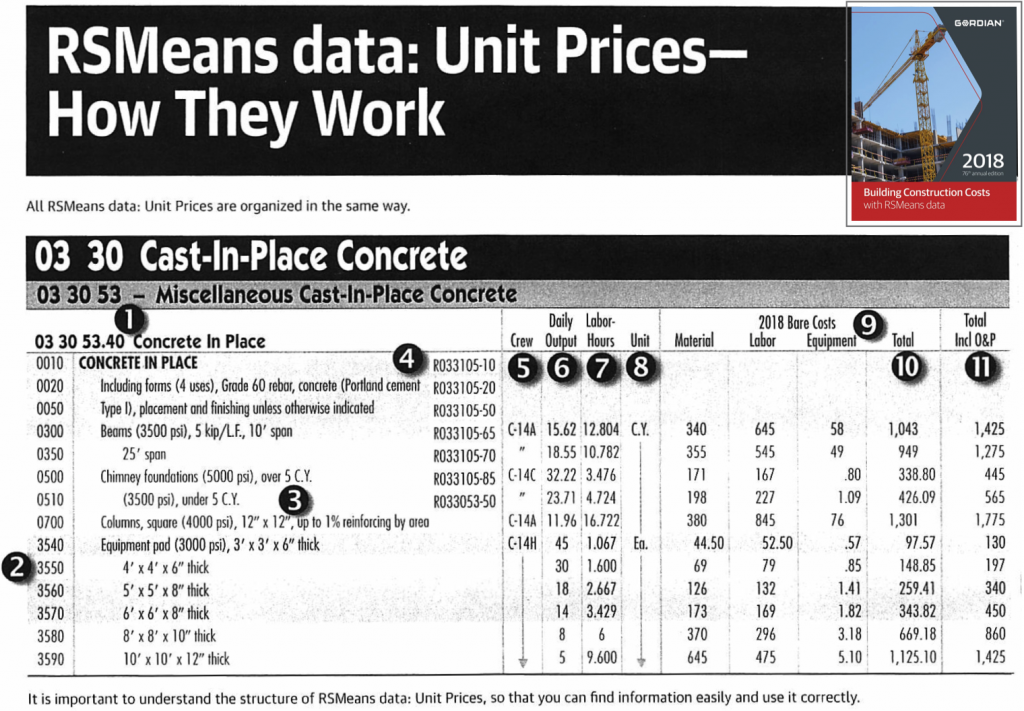
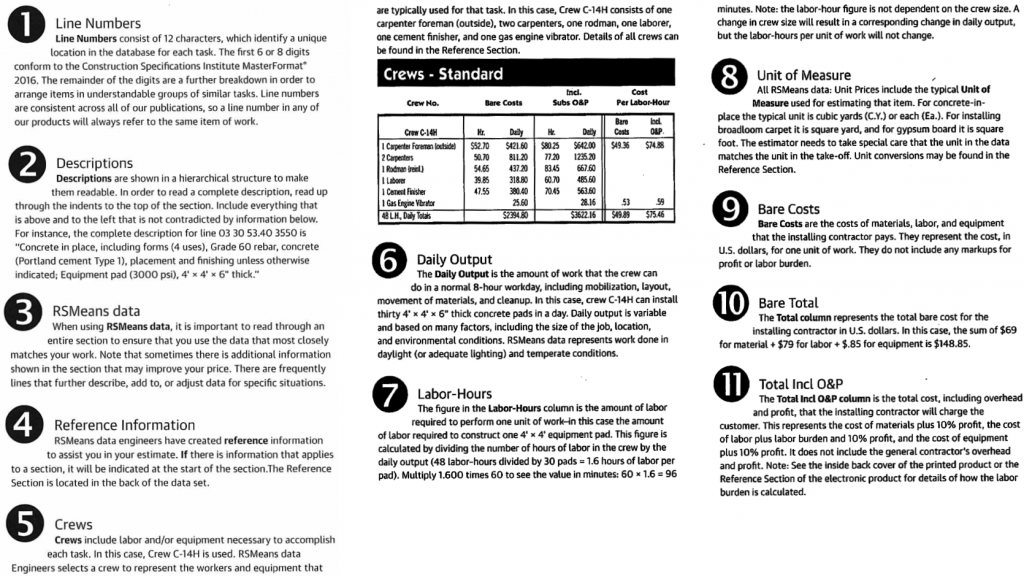
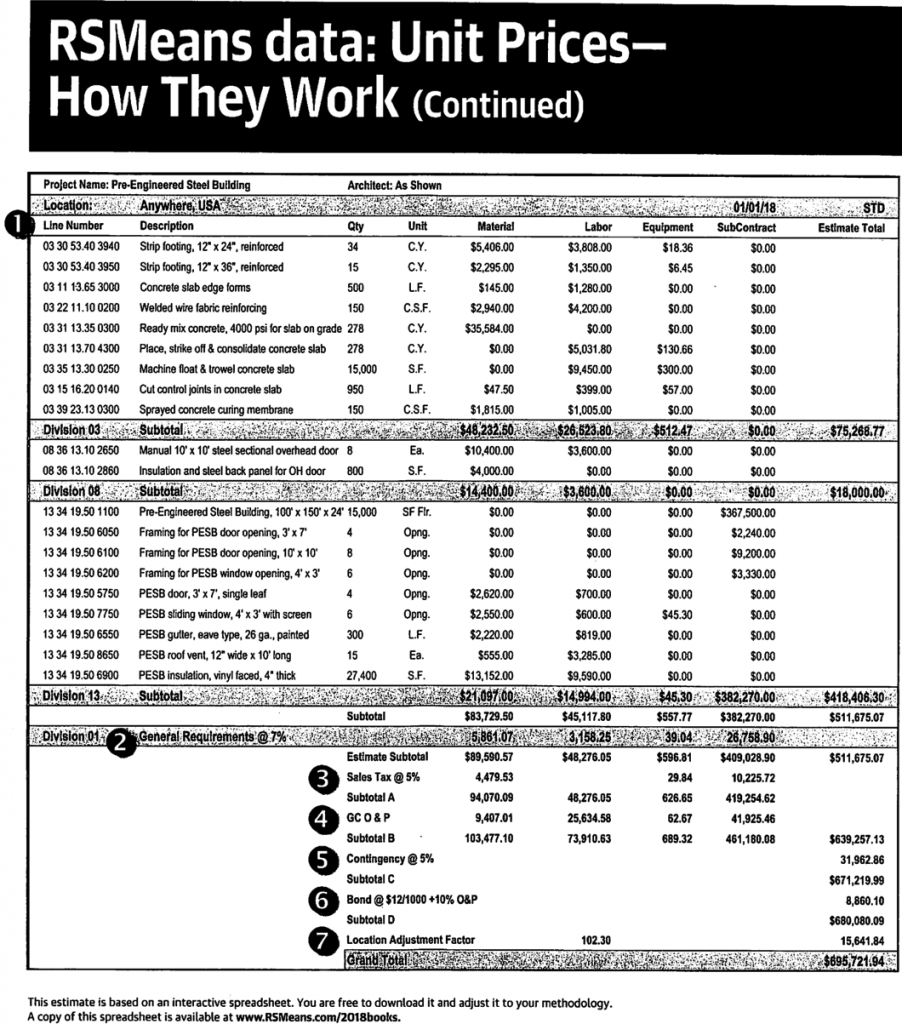
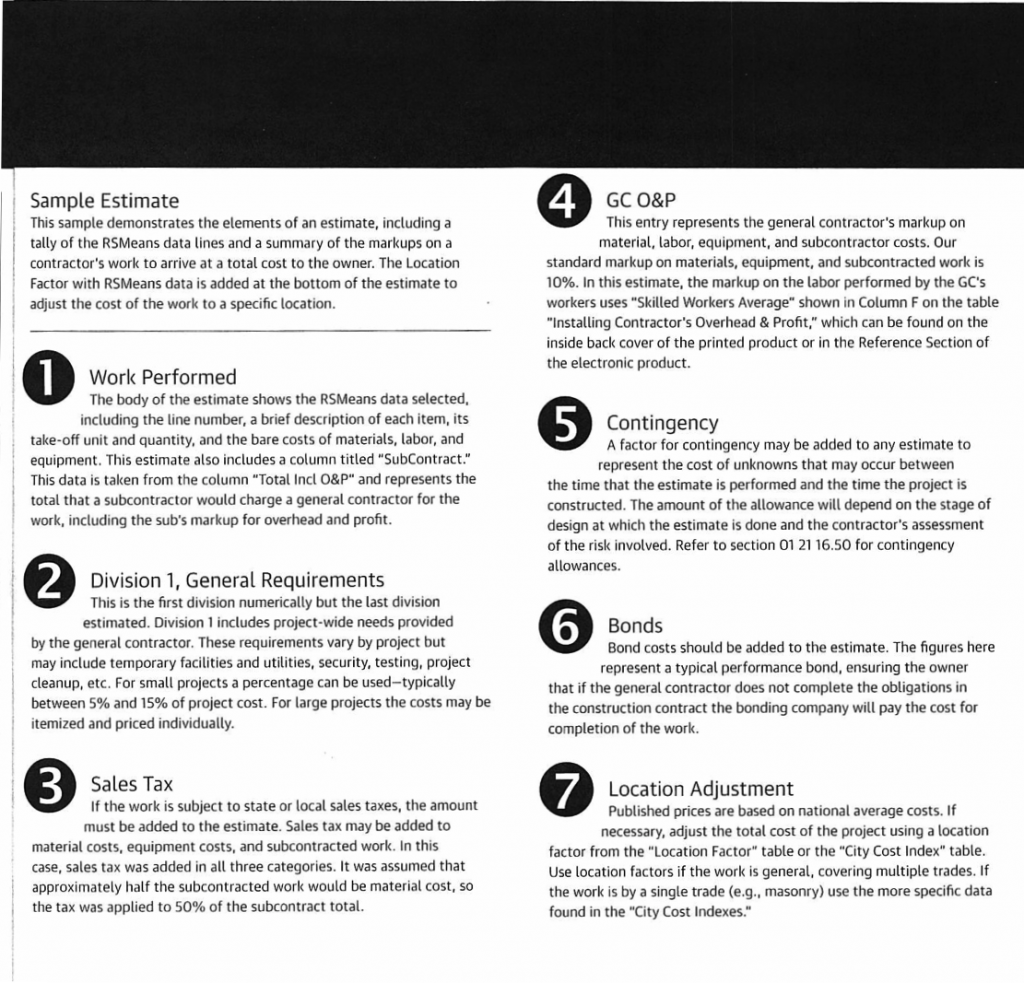
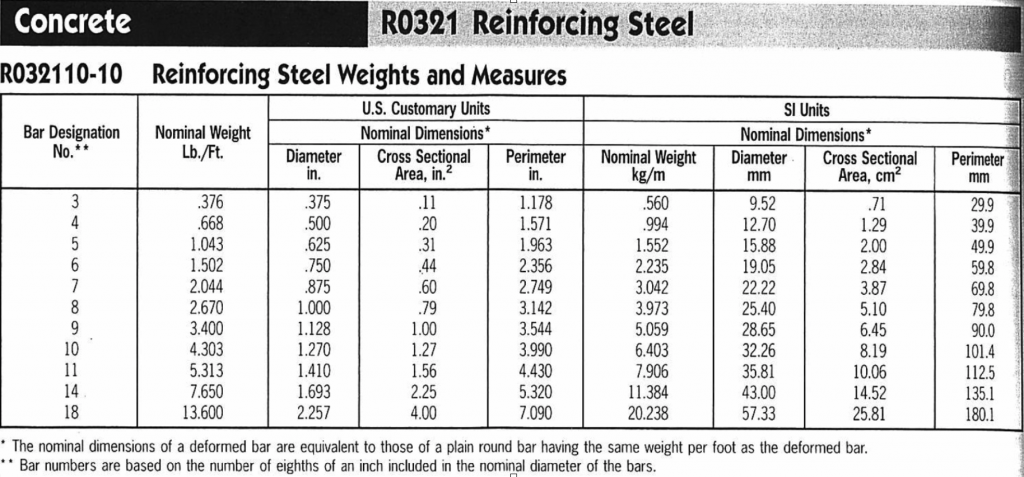
In addition to estimating a cost for an activity, the Gordian detailed cost guides (building construction, electrical, concrete, etc.) also provide information regarding production rates and crews for each of the cost elements. Figure 7 shows a typical crew that wold be used for an activity. In this example, the crew is a Crew B-92 which has 1 foreman, 3 laborers, and several pieces of equipment. The crew has both a bare cost per day ($1,819.60 in Figure 7) and a cost including overhead and profit. In the example, you can also see that there are 32 Labor Hours (LH) per day from this crew (4 people x 8 hours per day = 32 LH per day). The total cost per individual labor hour is also presented, e.g., for Crew B-92, the cost per average labor hour, including all equipment, overhead and profit, would be $79.63 (which is $2,548.04 / 32 LH). Therefore, if an estimator wanted to estimate by a labor hour, for either the initial estimate or change order, they could use the cost per average LH for this calculation.
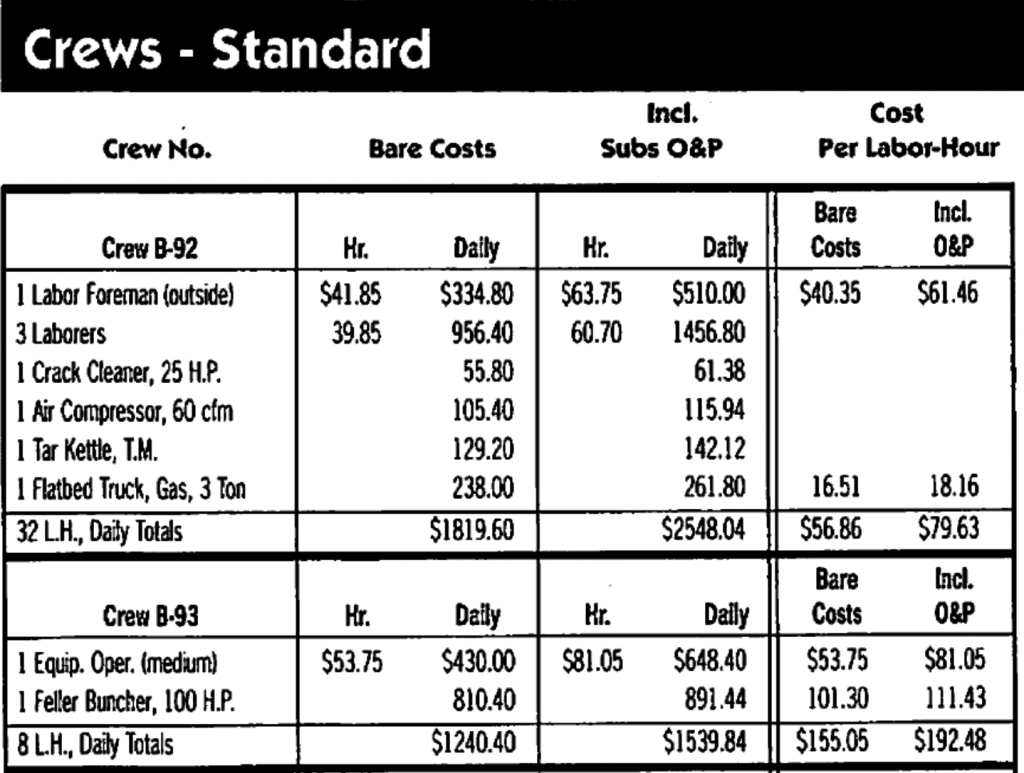
Additional Detailed Unit Price Resources
Gordian guides with R.S. Means data are not the only resources that can be used to develop detailed unit price estimates. Many companies maintain a database of their historical unit rates for common work tasks, and they will leverage these historical costs to develop future construction cost estimates. They may also review, in detail, a similar project or group of projects to review specific actual costs from previous projects. This is a very valuable approach to reviewing costs, but it is also essential to understand the context of the costs when estimating potential future work.
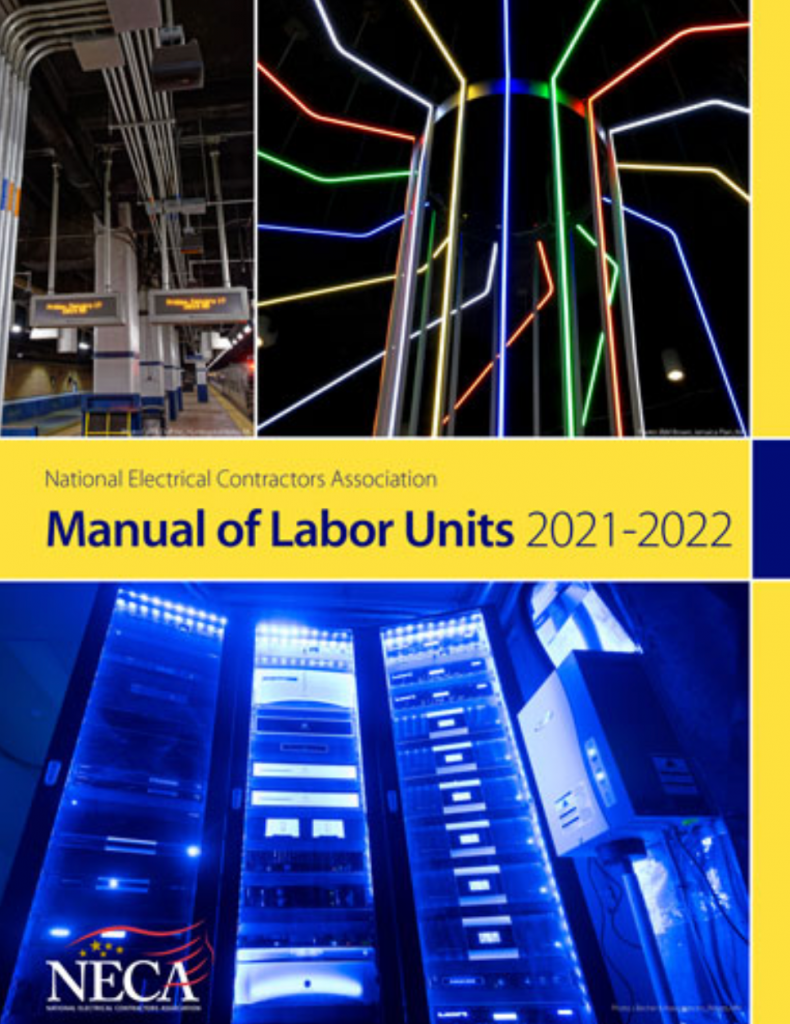
There are also several more specific cost estimating manuals that have been developed for specific trades. One commonly used guide for electrical work is the National Electrical Contractors Association (NECA) Manual of Labor Units (MLU) (see Figure 8). This Manual, developed by the trade association, publishes a typical labor unit for the detailed tasks performed by electrical workers and crews. The manual also uses a unique approach to quantifying the level of difficulty of the work activities and provides a different rate based on normal installation, difficult installation, and very difficult installation (see Figure 9 for definitions). To identify the difficulty classification, NECA has developed a Labor Factor Score Sheet (see Figure 10), which walks an estimator through a series of categories rated on a scale of 1 to 5 to develop an overall score for difficulty. This score is then used to select one of the three difficulty columns. The Manual includes a large number of electrical installation tasks. A sample page from the Manual is shown in Figure 11. It is important to note that the labor units are for direct work, and do not include costs for supervision.
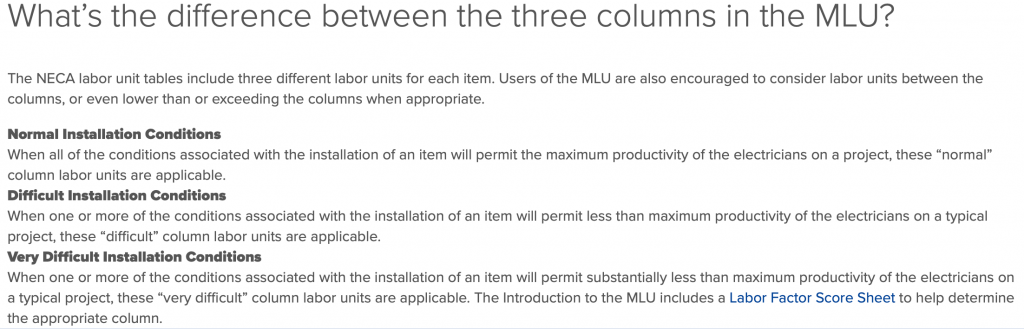
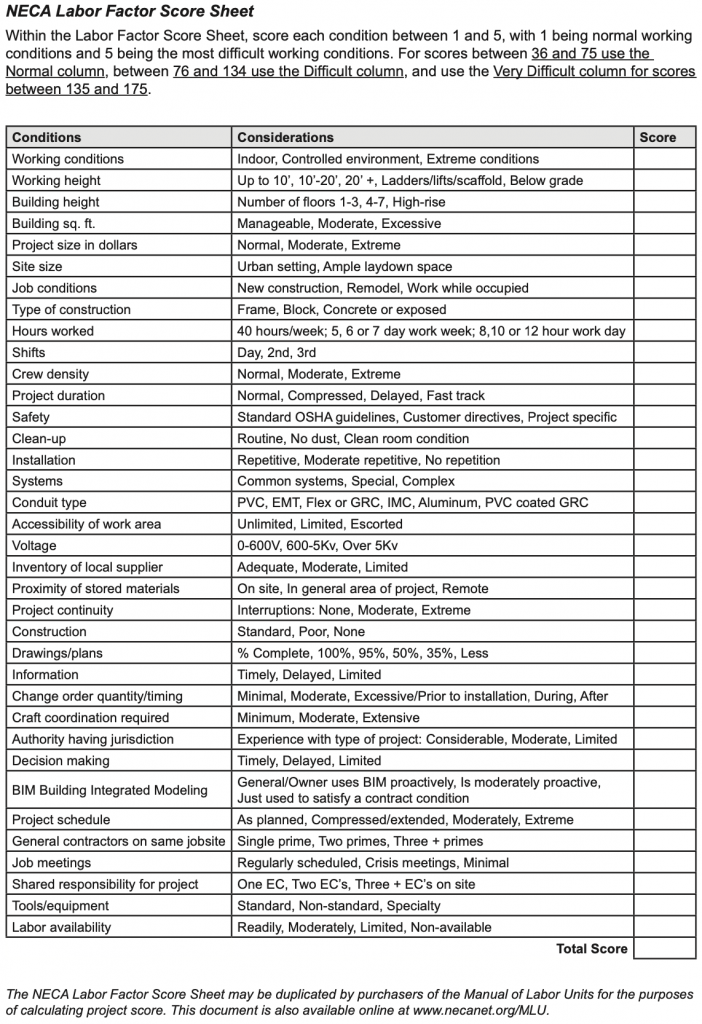
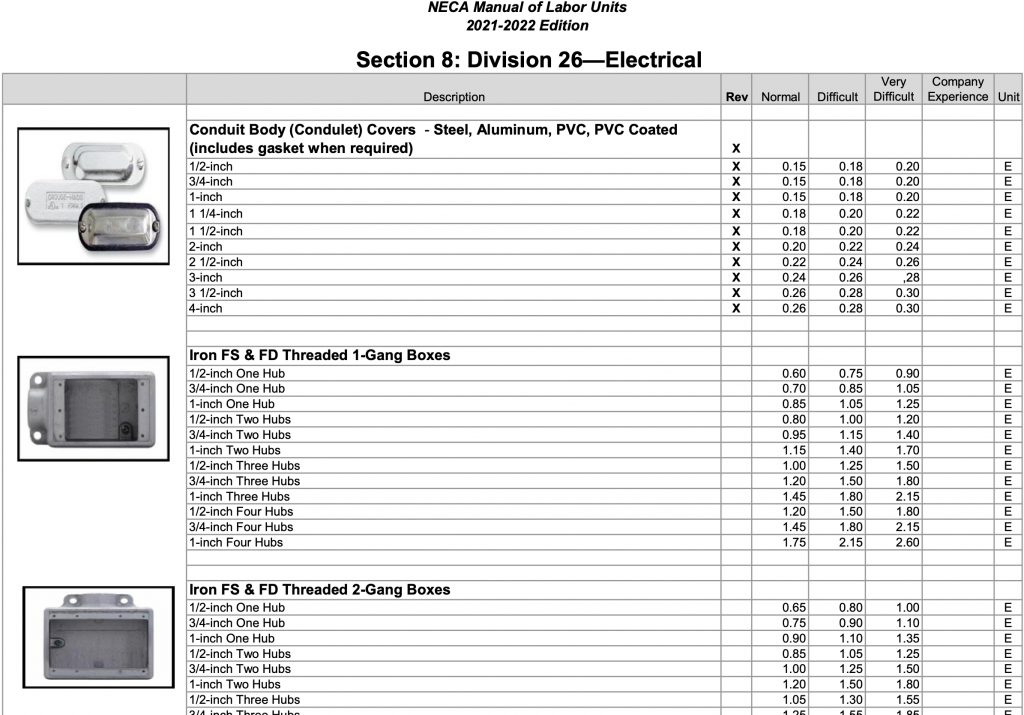
Other trades have similar resources, such as the online Mechanical Contractors of America Association (MCAA) Web-based Labor Estimating Manual, or the Sheet Metal and Air Conditioning Contractors’ National Association (SMACNA) Cost Reference Manual for Sheet Metal and HVAC. Many trade contractors will use these more detailed guides to calculate labor hours, and then apply multipliers to the labor hours based upon their perception of the project conditions, e.g., if it is a project that may support high levels of production due to prefabrication, good planning, and detailed modeling, they may apply a multiplier below 1.0. But, if the project will be challenging, they may apply multipliers above 1.0 when calculating the overall labor hours. These hours will then be combined with detailed estimates of material, equipment, overhead, and profit line items to calculate the overall cost estimate.
Review Questions