9.4 Comparing Traditional & Activity-based Costing
Calculating an accurate manufacturing cost for each product is a vital piece of information for a company’s decision-making. For example, knowing the cost to produce a unit of product affects not only how a business budgets to manufacture that product, but it is often the starting point in determining the sales price.
An important component in determining the total production costs of a product or job is the proper allocation of overhead. For some companies, the often less-complicated traditional method does an excellent job of allocating overhead. However, for many products, the allocation of overhead is a more complex issue, and an activity-based costing (ABC) system is more appropriate.
Another factor to consider in determining which of the two major overhead allocation methods to use is the cost associated with collecting and analyzing information. When making their decision regarding which method to use, the company must consider these costs, both in time and money. Table 9.4 compares overhead in the two systems. In many cases, the ABC method is more expensive in terms of time and other costs.
The difference between the traditional method (using one cost driver) and the ABC method (using multiple cost drivers) is more complex than simply the number of cost drivers. When direct labor is a large portion of the product cost, the overhead costs tend to be consistently driven by one cost driver, which is typically direct labor or machine hours; the traditional method appropriately allocates those costs. When technology is a large portion of the product cost, the overhead costs tend to be driven by multiple drivers, so using multiple cost drivers in the ABC method allows for a more precise allocation of overhead.
Traditional | ABC | |
---|---|---|
Overhead assigned | Single cost driver | Multiple cost drivers |
Optimal usage | When direct labor is a large portion of the product cost | When technology is a large portion of the product cost |
Orientation | Cost driven | Process driven |
As shown with Musicality’s products, not only are there different costs for each product when comparing traditional allocation with an activity-based costing, but ABC showed that the Solo product creates a loss for the company. Activity-based costing is a more accurate method, because it assigns overhead based on the activities that drive the overhead costs. It can be concluded, then, that the cost and subsequent gross loss for each unit’s sales provide a more accurate picture than the overall cost and gross profit under the traditional method. Table 9.4 compares the cost per unit using the different cost systems and shows how different the costs can be depending on the method used.
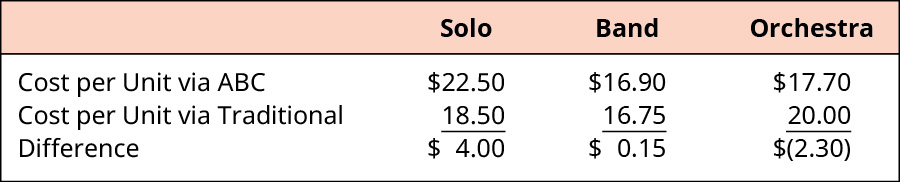
Advantages and Disadvantages of the Traditional Method of Calculating Overhead
The traditional allocation system assigns manufacturing overhead based on a single cost driver, such as direct labor hours, direct labor dollars, or machine hours, and is optimal when there is a relationship between the activity base and overhead. This most often occurs when direct labor is a large part of the product cost. The theory supporting the single cost driver is that the cost driver selected increases as overhead increases, and further analysis is more costly than it is valuable. Each method has its advantages and disadvantages. These are advantages of the traditional method:
- All manufacturing costs are classified as material, labor, or overhead and assigned to products regardless of whether they drive or are driven by production.
- All manufacturing costs are considered to be part of the product cost, whereas nonmanufacturing costs are not considered to be production costs and are not assigned to products, regardless of whether the costs are based on the products. For example, the machines used to receive and process customer orders are necessary because product orders must be taken, but their costs are not allocated to particular products.
- There is only one overhead cost pool and a single measure of activity, such as direct labor hours, which makes the traditional method simple and less costly to maintain. The predetermined overhead rate is based on estimated costs at the budgeted level of activity. Therefore, the overhead rate is consistent across products, but overhead may be over- or underapplied.
Disadvantages of the traditional method include:
- The use of the single cost driver does not allocate overhead as accurately as using multiple cost drivers.
- The use of the single cost driver may overallocate overhead to one product and underallocate overhead to another product, resulting in erroneous total costs and potentially setting an incorrect sales price.
- Traditional allocation assigns costs as period or product costs, and all product costs are included in the cost of inventory, which makes this method acceptable for generally accepted accounting principles (GAAP).
Advantages and Disadvantages of Creating an Activity-Based Costing System for Allocating Overhead
While ABC systems more accurately allocate the costs based on the various resources used to make the product, they cost more to use and, therefore, are not always the best method. Management needs to consider each system and how it will work within its own organization. Some advantages of activity-based costing include:
- There are multiple overhead cost pools, and each has its own unique measure of activity. This provides more accurate rates for applying overhead, but it takes more time to implement and results in a higher cost.
- The allocation bases (i.e., measures of activity) often differ from those used in traditional allocation. Multiple cost pools allow management to group costs being influenced by similar drivers and to consider cost drivers beyond the typical labor or machine hour. This results in a more accurate overhead application rate.
- The activity rates may consider the level of activity at capacity instead of the budgeted level of activity.
- Both nonmanufacturing costs and manufacturing costs may be assigned to products. The main rationale in assigning costs is the relationship between the cost and the product. If the cost increases as the volume of the product increases, it is considered part of overhead.
There are disadvantages to using ABC costing that management needs to consider when determining which method to use. Those disadvantages include:
- Some manufacturing costs may be excluded from product costs. For example, the cost to heat the factory may be excluded as a product cost because, while it is necessary for production, it does not fit into one of the activity-driven cost pools.
- It is more expensive, as there is a cost to collect and analyze cost driver information as well as to allocate overhead on the basis of multiple cost drivers.
- An ABC system takes much more to implement and operate, as information on cost drivers must be collected in an objective manner.
The advantages and disadvantages of both methods are as previously listed, but what is the practical impact on the product cost? There are several items to consider at the product costs level:
- Adopting an ABC overhead allocation system can allow a company to shift manufacturing overhead costs between products based on their volume.
- Using an ABC method to better assign unit-level, batch-level, product-level, and factory-level costs can increase the per-unit costs of the low-volume products and decrease the per-unit costs of the high-volume products.
- The effects are not symmetrical; there is usually a larger change in the per-unit costs of the low-volume products.
- The cost of the products may include some period costs but not some of the product costs, so it is not considered GAAP compliant. The information is supplemental and very helpful to management, but the company still needs to compute the product’s cost under the traditional method for financial reporting.