10.5 Fundamentals of Standard Costs
A syllabus is one way an instructor can communicate expectations to students. Students can use the syllabus to plan their studying to maximize their grade and to coordinate the amount and timing of studying for each course. Knowing what is expected, and when it is expected, allows for better plans and performance. When your performance does not match your expectations, a variance arises—a difference between the standard and the actual performance. You then need to determine why the difference occurred. You want to know why you did not receive the grade you expected so you can make adjustments for the next assignment to earn a better grade.
Companies operate in a similar manner. They have an expectation, or standard, for production. For example, if a company is producing tables, it might establish standards for such components as the amount of board feet of lumber expected to be used in producing each table or the number of hours of direct labor hours it expected to use in the table’s production. These standards can then be used in establishing standard costs that can be used in creating an assortment of different types of budgets.
When a variance occurs in its standards, the company investigates to determine the causes, so they can perform better in the future. For example, General Motors has standards for each item on a vehicle. It can determine the cost and selling price of a power antenna by knowing the standard material cost for the antenna and the standard labor cost of adding the antenna to the vehicle. General Motors also can add up all of the standard times for all vehicles it makes to determine if too much or too little labor was used in production.
Fundamentals of Standard Costs
It is important to establish standards for cost at the beginning of a period to prepare the budget; manage material, labor, and overhead costs; and create a reasonable sales price for a good. A standard cost is an expected cost that a company usually establishes at the beginning of a fiscal year for prices paid and amounts used. The standard cost is an expected amount paid for materials costs or labor rates. The standard quantity is the expected usage amount of materials or labor. A standard cost may be determined by past history or industry norms. The company can then compare the standard costs against its actual results to measure its efficiency. Sometimes when comparing standard costs against actual results, there is a difference.
This difference can be attributed to many reasons. For example, the coffee company mentioned in the opening vignette may expect to pay $0.50 per ounce for coffee grounds. After the company purchased the coffee grounds, it discovered it paid $0.60 per ounce. This variance would need to be accounted for, and possible operational changes would occur as a result. Cost accounting systems become more useful to management when they include budgeted amounts to serve as a point of comparison with actual results.
Many departments help determine standard cost. Product design, in conjunction with production, purchasing, and sales, determines what the product will look like and what materials will be used. Production works with purchasing to determine what material will work best in production and will be the most cost efficient. Sales will also help decide the material in terms of customer demand. Production will work with personnel to determine labor costs for the product, which is based on how long it will take to make the product, which departments will be involved, and what type and number of employees it will take.
Consider how many different materials can go into a product. For example, there are approximately 14,000 parts that comprise the average automobile. The manufacturer will set a standard price and a quantity used per automobile for each part, and it will determine the labor required to install the part. At Fiat Chrysler Automobiles’ Belvidere Assembly Plant, for example, there are approximately 5,000 employees assembling automobiles.2 In addition to having standard costs associated with each part, each employee has standards for the job he or she performs.
Standard costs are typically established for reasonably attainable levels of efficiency (production). They serve as a target and are useful in motivating standard performance. An ideal standard level is set assuming that everything is perfect, machines do not break down, employees show up on time, there are no defects, there is no scrap, and materials are perfect. This level of standard is not the best motivator, because employees may see this level as unattainable. For example, consider whether you would take a course if the letter grades were as follows: an A is 99–100%, a B is 98–99%, a C is 97–98%, a D is 96–97%, and below 96% is an F. These standards are unreasonable and unrealistic, and they would not motivate students to do well in the course.
At the other end of the spectrum, if the standards are too easy, there is little motivation to do better, and products may not be properly built, may be built with inferior materials, or both. For example, consider how you would handle the following grading scale for your course: an A is 50–100%, a B is 35–50%, a C is 10–35%, a D is 2–10%, and below 2% is an F. Would you learn anything? Would you try very hard? The same considerations come into play for employees with standards that are too easy.
Instead of these two extremes, a company would set an attainable standard, which is one that employees can reach with reasonable effort. The standards are not so high that employees will not try to reach them and not so low that they do not give any incentive for employees to achieve profitability.
In order for a company to establish its attainable standard cost for each product, it must consider the standard costs for materials, labor, and overhead. The material standard cost consists of a standard price per unit of material and a standard amount of material per unit. Returning to the opening vignette, let us say the coffee shop is trying to establish the standard materials cost for one cup of regular coffee. To keep the example simple, we are not incorporating the cost of water or the ceramic cup cost (since they are reused). Two components for the cup of coffee will need to be considered:
- Price per ounce of coffee grounds
- Amount of coffee grounds (materials) used per cup of coffee
To determine the standards for labor, the coffee shop would need to consider two additional components:
- Labor rate per minute
- Amount of time to make one cup of regular coffee
To determine the standard for overhead, the coffee shop would first need to consider the fact that it has two types of overhead as shown in Figure 10.28.
- Fixed overhead (does not change in total with production)
- Variable overhead (does change in total with production)
All of this information is entered on a standard cost card.

Once a company determines a standard cost, they can then evaluate any variances. A variance is the difference between a standard cost and actual performance. There are favorable and unfavorable variances. A favorable variance involves spending less, or using less, than the anticipated or estimated standard. An unfavorable variance involves spending more, or using more, than the anticipated or estimated standard. Before determining whether the variance is favorable or unfavorable, it is often helpful for the company to determine why the variance exists.
YOUR TURN
Developing a Standard Cost Card
Use the information provided to create a standard cost card for production of one deluxe bicycle from Bicycles Unlimited.
To make one bicycle it takes four pounds of material. The material can usually be purchased for $5.25 per pound. The labor necessary to build a bicycle consists of two types. The first type of labor is assembly, which takes 2.75 hours. These workers are paid $11.00 per hour. The second type of labor is finishing, which takes 4 hours. These workers are paid $15.00 per hour. Overhead is applied using labor hours. The variable overhead rate is $5.00 per labor hour. The fixed overhead rate is $3.00 per hour.
Solution
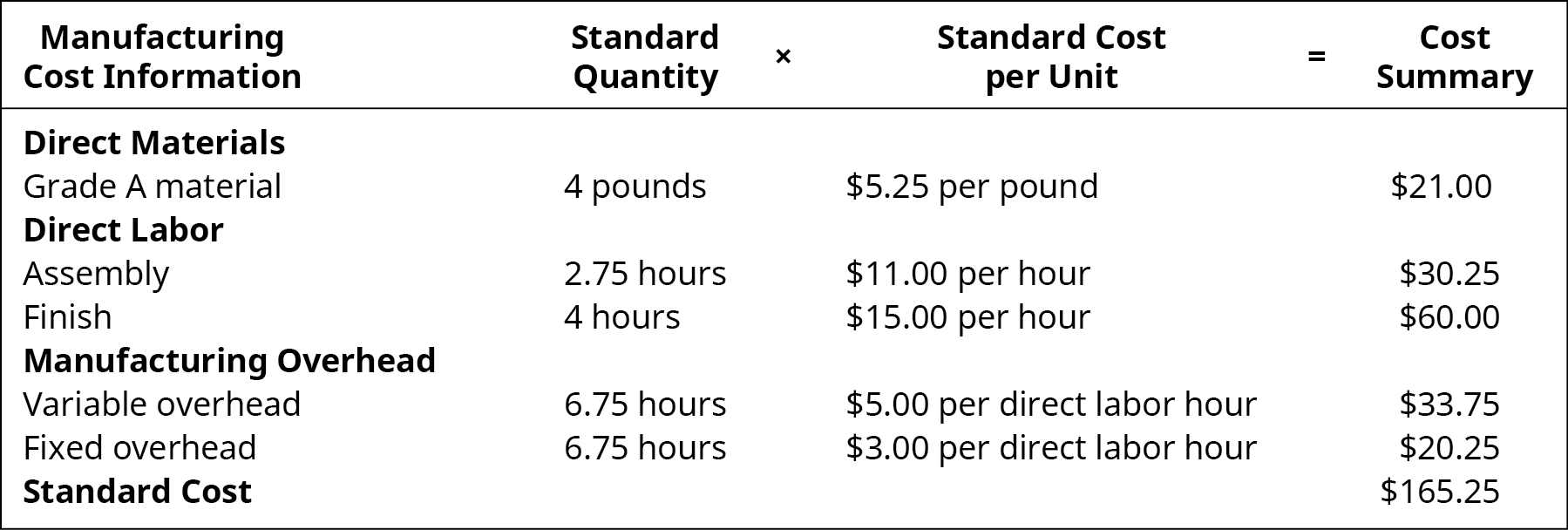
Different factors may produce a variance. The company could have paid too much or too little for production. It may have purchased the wrong grade of material or hired employees with more or less experience than required. Sometimes the variances are interrelated. For example, purchasing substandard materials may lead to using more time to make the product and may produce more scrap. The substandard material may have been more difficult to work with or had more defects than the proper grade material. In such a situation, a favorable material price variance could cause an unfavorable labor efficiency variance and an unfavorable material quantity variance. Employees who do not have the expected experience level may save money in the wage rate but may require more hours to be worked and more material to be used because of their inexperience.
Another situation in which a variance may occur is when the cost of labor and/or material changes after the standard was established. Toward the end of the fiscal year, standards often become less reliable because time has passed and the environment has changed. It is not reasonable to expect the price of all materials and labor to remain constant for 12 months. For example, the grade of material used to establish the standard may no longer be available.
Manufacturing Cost Variances
As you’ve learned, the standard price and standard quantity are anticipated amounts. Any change from these budgeted amounts will produce a variance. There can be variances for materials, labor, and overhead. Direct materials may have a variance in price of materials or quantity of materials used. Direct labor may have a variance in the rate paid to workers or the amount of time used to make a product. Overhead may produce a variance in expected fixed or variable costs, leading to possible differences in production capacity and management’s ability to control overhead. More specifics on the formulas, processes, and interpretations of the direct materials, direct labor, and overhead variances are discussed in each of this chapter’s following sections.
CONCEPTS IN PRACTICE
Qualcomm3
Qualcomm Inc. is a large producer of telecommunications equipment focusing mainly on wireless products and services. As with any company, Qualcomm sets labor standards and must address any variances in labor costs to stay on budget, and control overall manufacturing costs.
In 2018, Qualcomm announced a reduction to its labor force, affecting many of its full-time and temporary workers. The reduction in labor was necessary to suppress rising expenses that could not be controlled through overhead or materials cost-cutting measures. The variances between standard labor rates and actual labor rates, and diminishing profit margins will have contributed to this decision. It is important for Qualcomm management to keep labor variances minimal in the future so that large workforce reductions are not required to control costs.
Long Description
Standard Cost Card. Product: 1 Cup of Coffee. Manufacturing Cost Information, Standards. Quantity x Standard Cost per Unit equals Cost Summary. Direct Materials (Coffee grounds), .5 ounces, $0.50 per ounce, $0.25. Direct Labor Barista, 1 minute, $0.20 per minute, $0.20. Manufacturing Overhead Variable, 1 minute, $0.50 per direct labor minute, $0.05. Manufacturing Overhead Fixed, 1 minute, $0.10 per direct labr minute, $0.10. Total, -, -, $0.60 Return
Manufacturing Cost Information: Standard Quantity times Standard Cost per Unit equals Cost Summary. Direct Materials Grade A material, 4 pounds, $5.25 per pound, $21.00. Direct Labor Assembly, 2.75 hours, $11.00 per hour, $30.25. Direct Labor Finish, 4 hours, $15.00 per hour, $60.00. Manufacturing Overhead Variable, 6.75 hours, $5.00 per direct labor hour, $33.75. Manufacturing Overhead Fixed, 6.75 hours, $3.00 per direct labor hour, $20.25. Standard Cost, -, -, $165.25. Return
Footnotes
- 2 “Belvidere Assembly Plant and Belvidere Satellite Stamping Plant.” Fiat Chrysler Automobiles. June 2018. http://media.fcanorthamerica.com/newsrelease.do?id=323&mid=1
- 3 Munsif Vengattil. “Qualcomm Begins Layoffs as Part of Cost Cuts.” Reuters. April 18, 2018. https://www.reuters.com/article/us-qualcomm-layoffs/qualcomm-begins-layoffs-as-part-of-cost-cuts-idUSKBN1HP33L