10.9 Management’s Use of Variance Analysis
Companies use variance analysis in different ways. The starting point is the determination of standards against which to compare actual results. Many companies produce variance reports, and the management responsible for the variances must explain any variances outside of a certain range. Some companies only require that unfavorable variances be explained, while many companies require both favorable and unfavorable variances to be explained.
Requiring managers to determine what caused unfavorable variances forces them to identify potential problem areas or consider if the variance was a one-time occurrence. Requiring managers to explain favorable variances allows them to assess whether the favorable variance is sustainable. Knowing what caused the favorable variance allows management to plan for it in the future, depending on whether it was a one-time variance or it will be ongoing.
Another possibility is that management may have built the favorable variance into the standards. Management may overestimate the material price, labor rate, material quantity, or labor hours per unit, for example. This method of overestimation, sometimes called budget slack, is built into the standards so management can still look good even if costs are higher than planned. In either case, managers potentially can help other managers and the company overall by noticing particular problem areas or by sharing knowledge that can improve variances.
Often, management will manage “to the variances,” meaning they will make decisions that may not be advantageous to the company’s best interests over the long run, in order to meet the variance report threshold limits. This can occur when the standards are improperly established, causing significant differences between actual and standard numbers.
Management can use standard costs to prepare the budget for the upcoming period, using the past information to possibly make changes to production elements. Standard costs are a measurement tool and can thus be used to evaluate performance. As you’ve learned, management may manage “to the variances” and can manipulate results to meet expectations. To reduce this possibility, performance should be measured on multiple outcomes, not simply on standard cost variances.
As shown in Table 10.3, standard costs have pros and cons to consider when using them in the decision-making and evaluation processes.
Pros | Cons |
---|---|
|
|
Standard costing provides many benefits and challenges, and a thorough analysis of each variance and the possible unfavorable or favorable outcomes is required to set future expectations and adjust current production goals.
The following is a summary of all direct materials variances (Figure 10.66), direct labor variances (Figure 10.67), and overhead variances (Figure 10.68) presented as both formulas and tree diagrams. Note that for some of the formulas, there are two presentations of the same formula, for example, there are two presentations of the direct materials price variance. While both arrive at the same answer, students usually prefer one formula structure over the other.
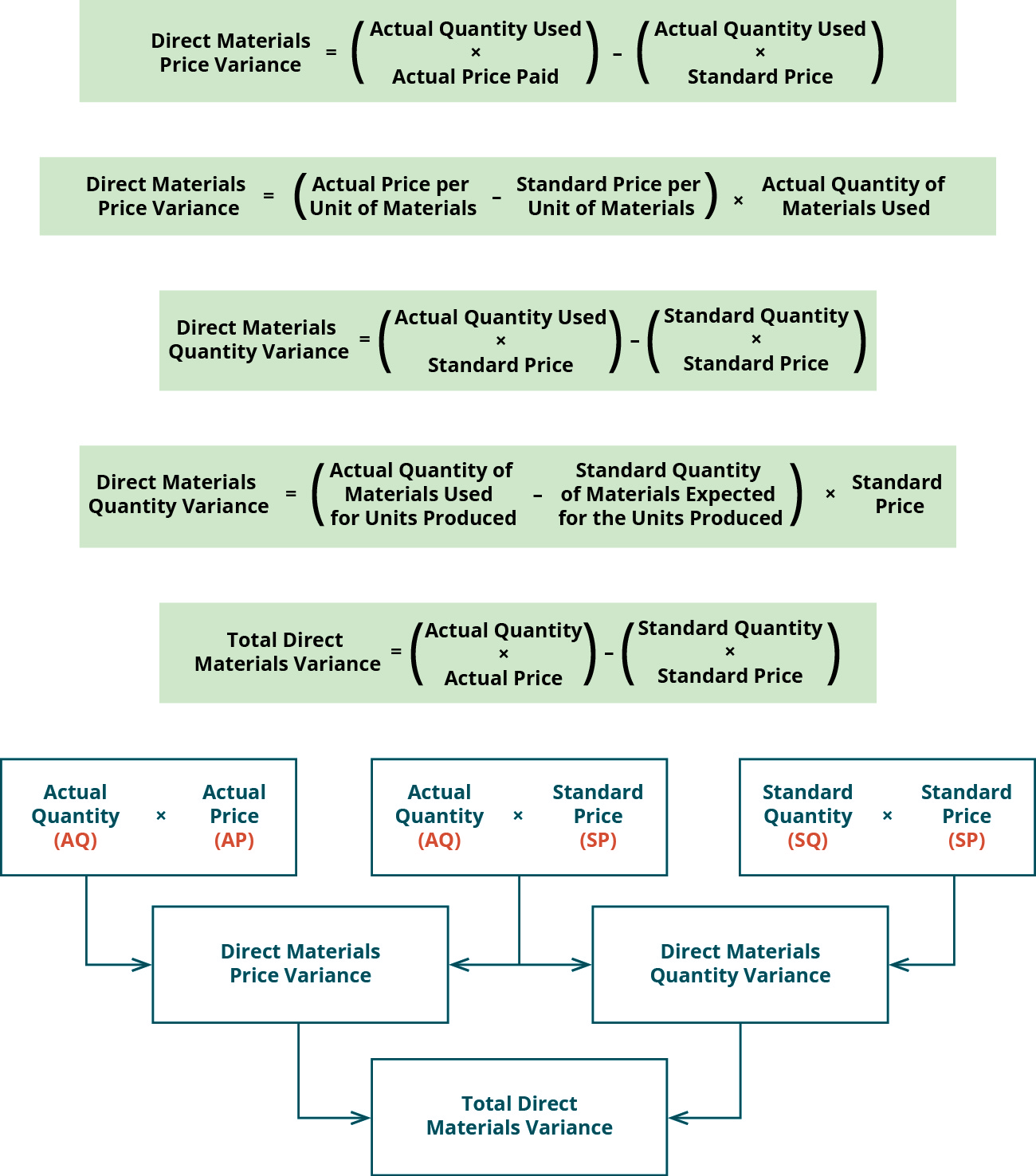
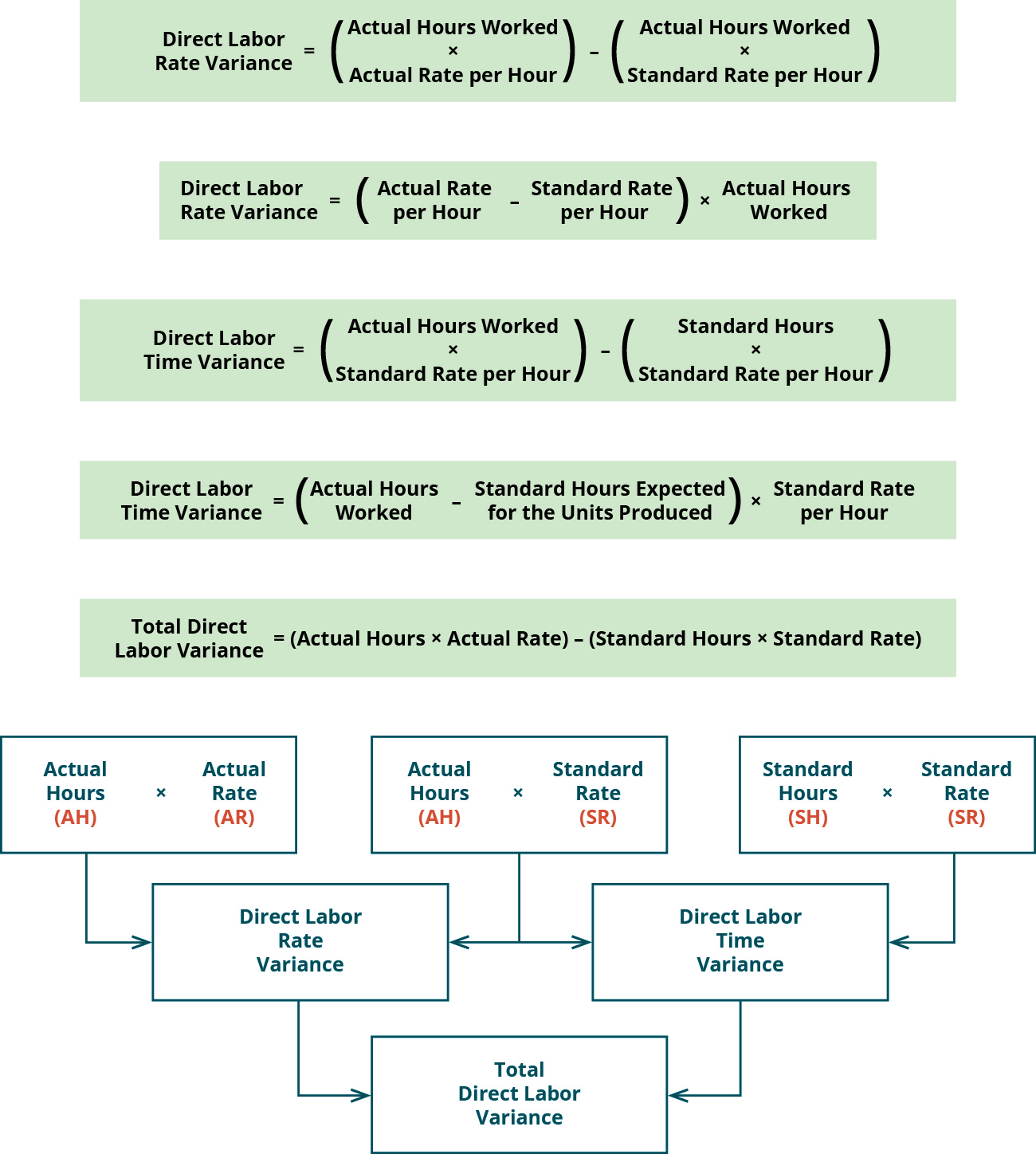
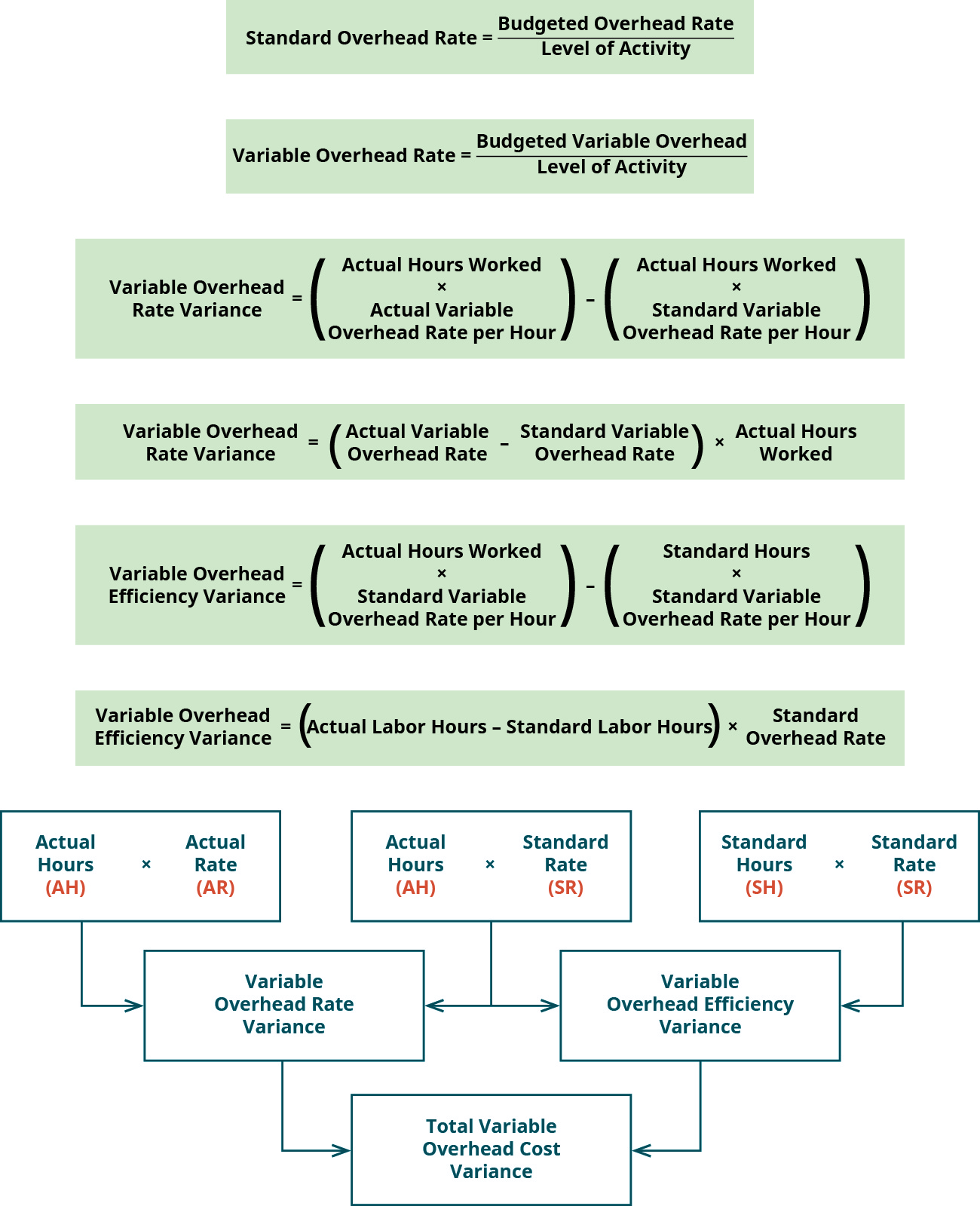
YOUR TURN
Barley, Inc. Production
Barley, Inc., produces a product and has the following as standard costs per unit for materials and labor:
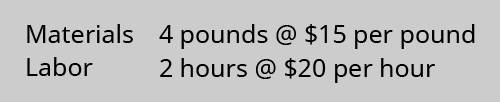
For the month of October, the following information was gathered related to production:
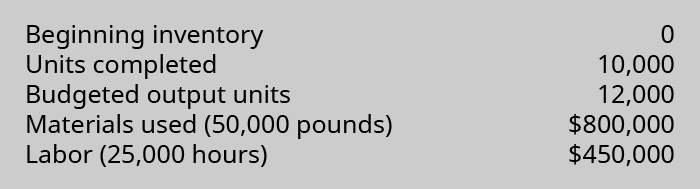
Compute:
- The materials price and quantity variances
- The labor rate and efficiency variances
Provide possible explanations for each variance.
Solution
A.
Materials price variance:
$50,000 unfavorable = ($16* – $15) × 50,000 lb.
*$800,000 ÷ 50,000
An unfavorable materials price variance occurred because the actual cost of materials was greater than the expected or standard cost. This could occur if a higher-quality material was purchased or the suppliers raised their prices.
Materials quantity variance:
$150,000 unfavorable = (50,000 lb. – 40,000* lb.) × $15 per lb.
*4 lb. × 10,000 units
An unfavorable materials quantity variance occurred because the pounds of materials used were greater than the pounds expected to be used. This could occur if there were inefficiencies in production or the quality of the materials was such that more needed to be used to meet safety or other standards.
Materials inputs:
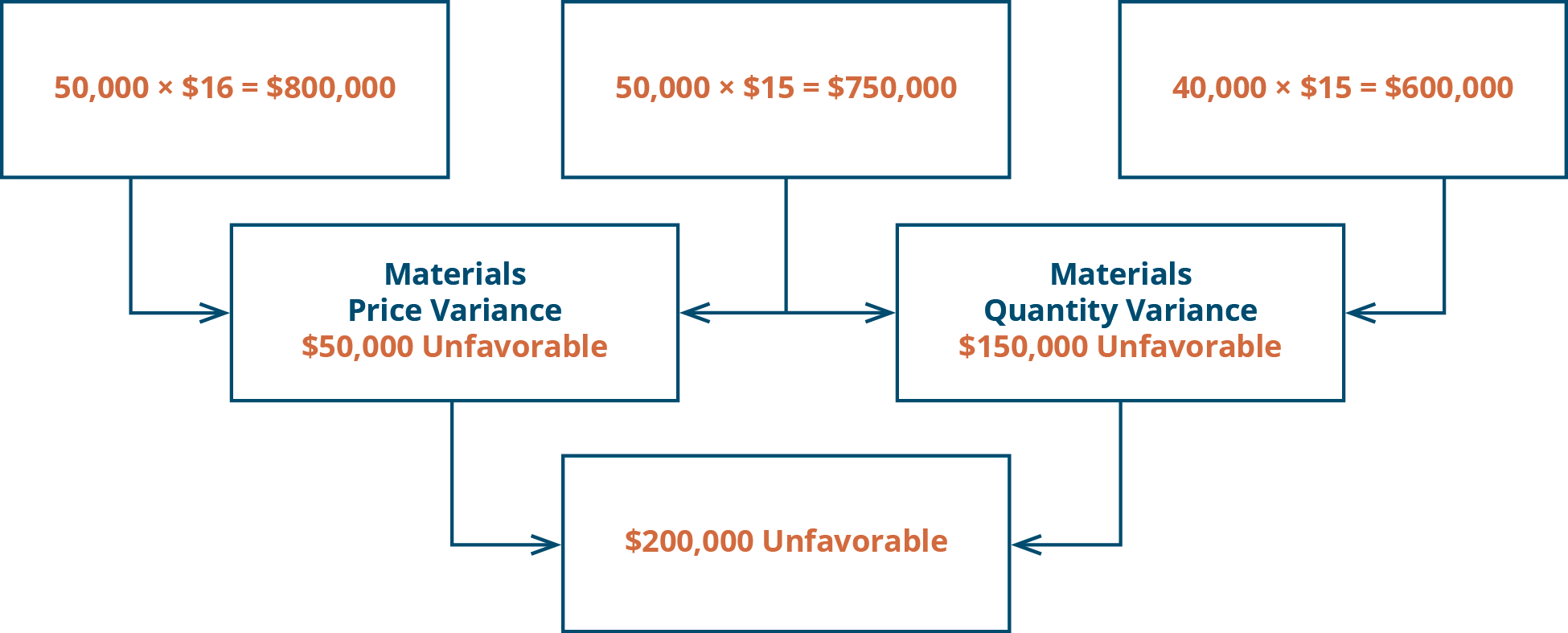
B.
Labor rate variance:
$50,000 favorable = ($18* per hour – $20 per hour) × 25,000 hours
*$450,000 ÷ 25,000
A favorable labor rate variance occurred because the rate paid per hour was less than the rate expected to be paid (standard) per hour. This could occur because the company was able to hire workers at a lower rate, because of negotiated union contracts, or because of a poor labor rate estimate used in creating the standard.
Labor quantity variance:
$100,000 unfavorable = (25,000 hours – 20,000* hours) × $20 per hour
*2 hours × 10,000 units
An unfavorable labor quantity variance occurred because the actual hours worked to make the 10,000 units were greater than the expected hours to make that many units. This could occur because of inefficiencies of the workers, defects and errors that caused additional time reworking items, or the use of new workers who were less efficient.
Labor inputs:
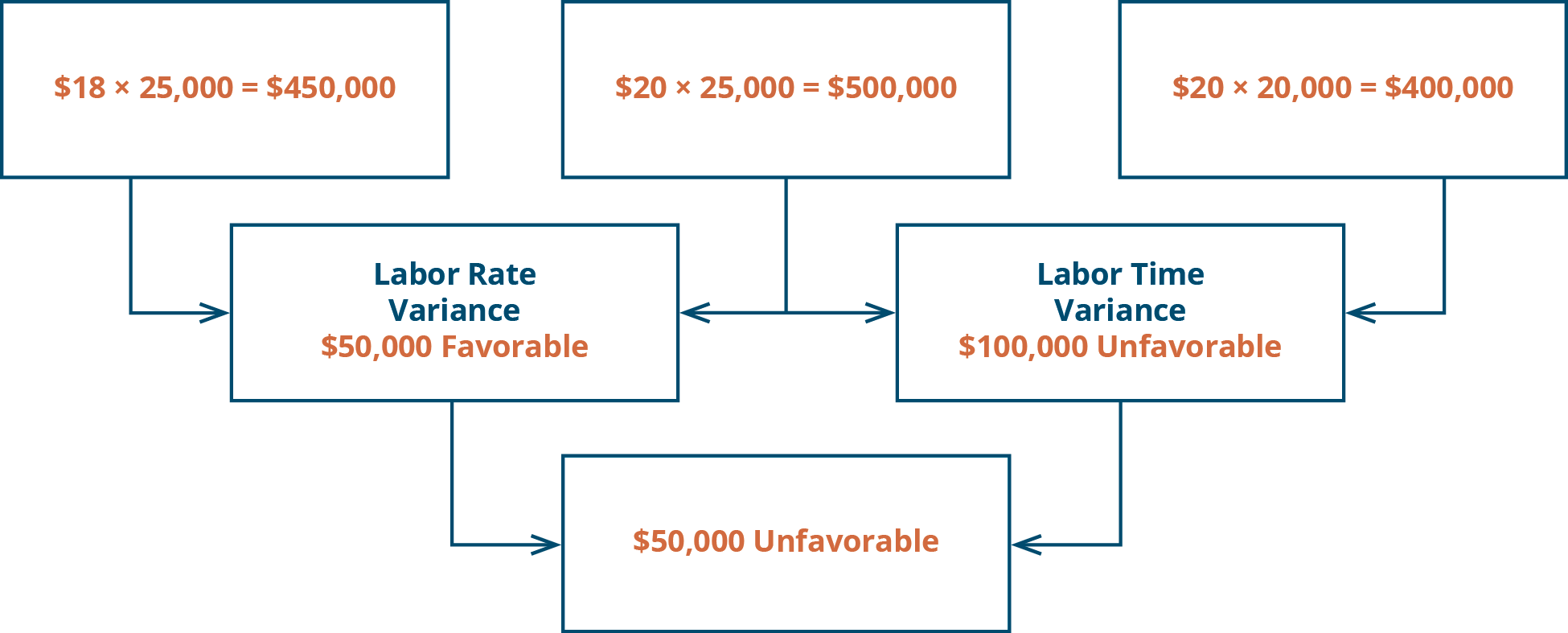
Long Description
Direct Materials Price Variance equals (Actual Quantity Used times Actual Price Paid) minus (Actual Quantity Used times Standard Price). Direct Materials Price Variance equals (Actual Price per Unit of Materials minus Standard Price per Unit of Materials) times Actual Quantity of Materials Used. Direct Materials Quantity Variance equals (Actual Quantity Used times Standard Price) minus (Standard Quantity times Standard Price). Direct Materials Quantity Variance equals (Actual Quantity of Materials Used for Units Produced minus Standard Quantity of Materials Expected for the Units Produced) times Standard Price. Total Direct Material Variance equals (Actual Quantity times Actual Price) minus (Standard Quantity times Standard Price). There are three top row boxes. Two, Actual Quantity (AQ) times Actual Price (AP) and Actual Quantity (AQ) times Standard Price (SP) combine to point to a Second row box: Direct Material Price Variance. Two top row boxes: Actual Quantity (AQ) times Standard Price (SP) and Standard Quantity (SQ) times Standard Price (SP) combine to point to Second row box: Direct Materials Quantity Variance. Notice the middle top row box is used for both of the variances. Second row boxes: Direct Material Price Variance and Direct Materials Quantity Variance combine to point to bottom row box: Total Direct Material Variance. Return
Direct Labor Rate Variance equals (Actual Hours Worked times Actual Rate per Hour) minus (Actual Hours Worked times Standard Rate per Hour). Direct Labor Rate Variance equals (Actual Rate per Hour minus Standard Rate per Hour) times Actual Hours Worked. Direct Labor Time Variance equals (Actual Hours Worked times Standard rate per Hour) minus (Standard Hours times Standard Rate per Hour). Direct Labor Time Variance equals (Actual Hours Worked minus Standard Hours Expected for the Units Produced) times Standard Rate per Hour. Total Direct Labor Variance minus (Actual Hours times Actual Rate) minus (Standard Hours times Standard Rate). There are three top row boxes. Two, Actual Hours (AH) times Actual Rate (AR) and Actual Hours (AH) times Standard Rate (SR) combine to point to a Second row box: Direct Labor Rate Variance. Two top row boxes: Actual Hours (AH) times Standard Rate (SR) and Standard Hours (SH) times Standard Rate (SR) combine to point to Second row box: Direct Labor Time Variance. Notice the middle top row box is used for both of the variances. Second row boxes: Direct Labor Rate Variance and Direct Labor Time Variance combine to point to bottom row box: Total Direct Labor Variance. Return
Standard Overhead Rate equals Budgeted Overhead Rate divided by Level of Activity. Variable Overhead Rate equals Budgeted Variable Overhead divided by Level of Activity. Variable Overhead Rate Variance equals (Actual Hours Worked times Actual Variable Overhead Rate per Hour) minus (Actual Hours Worked times Standard Variable Overhead Rate per Hour). Variable Overhead Rate Variance equals (Actual Variable Overhead Rate minus Standard Variable Overhead Rate) times Actual Hours Worked. Variable Overhead Efficiency Variance equals Actual Hours Worked times Standard Variable Overhead Rate per Hour) minus (Standard Hours times Standard Variable Overhead rate per Hour). Variable Overhead Efficiency Variance equals Actual Labor Hours minus Standard Labor Hour) times Standard Overhead Rate. There are three top row boxes. Two, Actual Hours (AH) times Actual Rate (AR) and Actual Hours (AH) times Standard Rate (SR) combine to point to a Second row box: Variable Overhead Rate Variance. Two top row boxes: Actual Hours (AH) times Standard Rate (SR) and Standard Hours (SH) times Standard Rate (SR) combine to point to Second row box: Variable Overhead Efficiency Variance. Notice the middle top row box is used for both of the variances. Second row boxes: Variable Overhead Rate Variance and Variable Overhead Efficiency Variance combine to point to bottom row box: Total Variable Overhead Cost Variance Return