8.3 Three Major Components of Product Costs in Job Order
In order to set an appropriate sales price for a product, companies need to know how much it costs to produce an item. Just as a company provides financial statement information to external stakeholders for decision-making, they must provide costing information to internal managerial decision makers. Virtually every tangible product has direct materials, direct labor, and overhead costs that can include indirect materials and indirect labor, along with other costs, such as utilities and depreciation on production equipment. To account for these and inform managers making decisions, the costs are tracked in a cost accounting system.
While the flow of costs is generally the same for all costing systems, the difference is in the details: Product costs have material, labor, and overhead costs, which may be assessed differently. In most production facilities, the raw materials are moved from the raw materials inventory into the work in process inventory. The work in process involves one or more production departments and is where labor and overhead convert the raw materials into finished goods. The movement of these costs through the work in process inventory is shown in Figure 8.15.

At this stage, the completed products are transferred into the finished goods inventory account. When the product is sold, the costs move from the finished goods inventory into the cost of goods sold.
While many types of production processes could be demonstrated, let’s consider an example in which a contractor is building a home for a client. The accounting system will track direct materials, such as lumber, and direct labor, such as the wages paid to the carpenters constructing the home. Along with these direct materials and labor, the project will incur manufacturing overhead costs, such as indirect materials, indirect labor, and other miscellaneous overhead costs. Samples of these costs include indirect materials, such as nails, indirect labor, such as the supervisor’s salary, assuming that the supervisor is overseeing several projects at the same time, and miscellaneous overhead costs such as depreciation on the equipment used in the construction project.
As direct materials, direct labor, and overhead are introduced into the production process, they become part of the work in process inventory value. When the home is completed, the accumulated costs become part of the finished goods inventory value, and when the home is sold, the finished goods value of the home becomes the cost of goods sold. Figure 8.16 illustrates the flow of these costs through production.
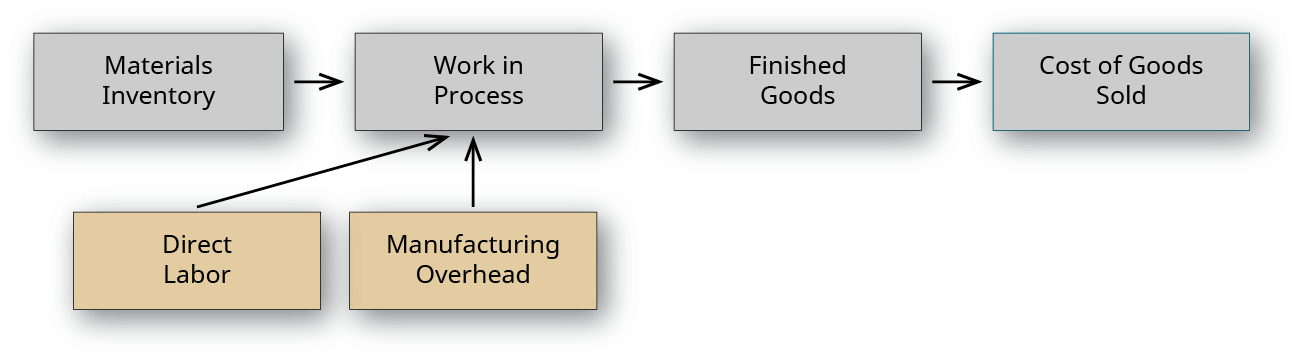
The three general categories of costs included in manufacturing processes are direct materials, direct labor, and overhead. Note that there are a few exceptions, since some service industries do not have direct material costs, and some automated manufacturing companies do not have direct labor costs. For example, a tax accountant could use a job order costing system during tax season to trace costs. The one major difference between the home builder example and this one is that the tax accountant will not have direct material costs to track. The few assets used will typically be categorized as overhead.
A benefit of knowing the production costs for each job in a job order costing system is the ability to set appropriate sales prices based on all the production costs, including direct materials, direct labor, and overhead. The unique nature of the products manufactured in a job order costing system makes setting a price even more difficult. For each job, management typically wants to set the price higher than its production cost. Even if management is willing to price the product as a loss leader, they still need to know how much money will be lost on each product. To achieve this, management needs an accounting system that can accurately assign and document the costs for each product.
If you’re not familiar with the concept of a loss leader, a simple example might help clarify the concept. A loss leader is a product that is sold at a price that is often less than the cost of producing it in order to entice you to buy accessories that are necessary for its use. For example, you might pay $50 or $60 for a printer (for which the producer probably does not make any profit) in order to then sell you extremely expensive printer cartridges that only print a few pages before they have to be replaced. However, even pricing a product as a loss leader requires analysis of the three categories of costs: direct materials, direct labor, and overhead.
Direct Materials
Direct materials are those materials that can be directly traced to the manufacturing of the product. Some examples of direct materials for different industries are shown in Table 8.2 In order to respond quickly to production needs, companies need raw materials inventory on hand. While production volume might change, management does not want to stop production to wait for raw materials to be delivered. Further, a company needs raw materials on hand for future jobs as well as for the current job. The materials are sent to the production department as it is needed for production of the products.
Industry | Direct Materials |
---|---|
Automotive | Iron, aluminum, glass, rubber |
Cell phones | Glass, various metals, plastic |
Furniture | Wood, leather, vinyl |
Jewelry | Gold, silver, diamonds, rubies |
Pharmaceuticals | Natural or synthetic biological ingredients |
Each job begins when raw materials are put into the work in process inventory. When the materials are requested for production, a materials requisition slip is completed and shows the exact items and quantity requested, along with the associated cost. The completed form is signed by the requestor and approved by the manager responsible for the budget.
Returning to the example of Dinosaur Vinyl’s order for Macs & Cheese’s stadium sign, Figure 8.17 shows the materials requisition form for Job MAC001. This form indicates the quantity and specific items to be put into the work in process. It also transfers the cost of those items to the work in process inventory and decreases the raw materials inventory by the same amount. The raw materials inventory department maintains a copy to document the change in inventory levels, and the accounting department maintains a copy to properly assign the costs to the particular job.
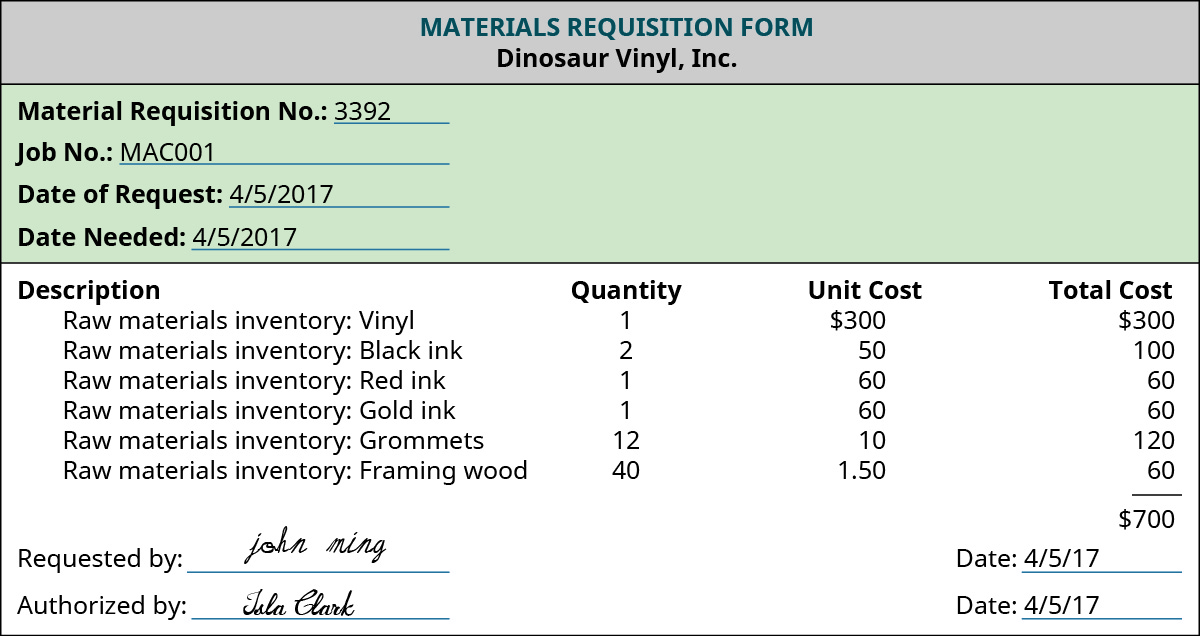
Dinosaur Vinyl has a beginning inventory of $1,000 in raw materials: vinyl, and $300 in each of its ink inventories: raw materials: black ink, raw materials: red ink, and raw materials: gold ink. In order to have enough inventory on hand for all of its jobs, it purchases $10,000 in vinyl and $500 in black ink. The T-accounts in Figure 8.18 show the stated beginning debit balances. An additional $10,000 of vinyl and $500 of black ink were then purchased for anticipated use, providing the demonstrated final account balances. The red ink and gold ink balances did not change, since no additional quantities were purchased.
The beginning balances and purchases in each of these accounts are illustrated in Figure 8.18.
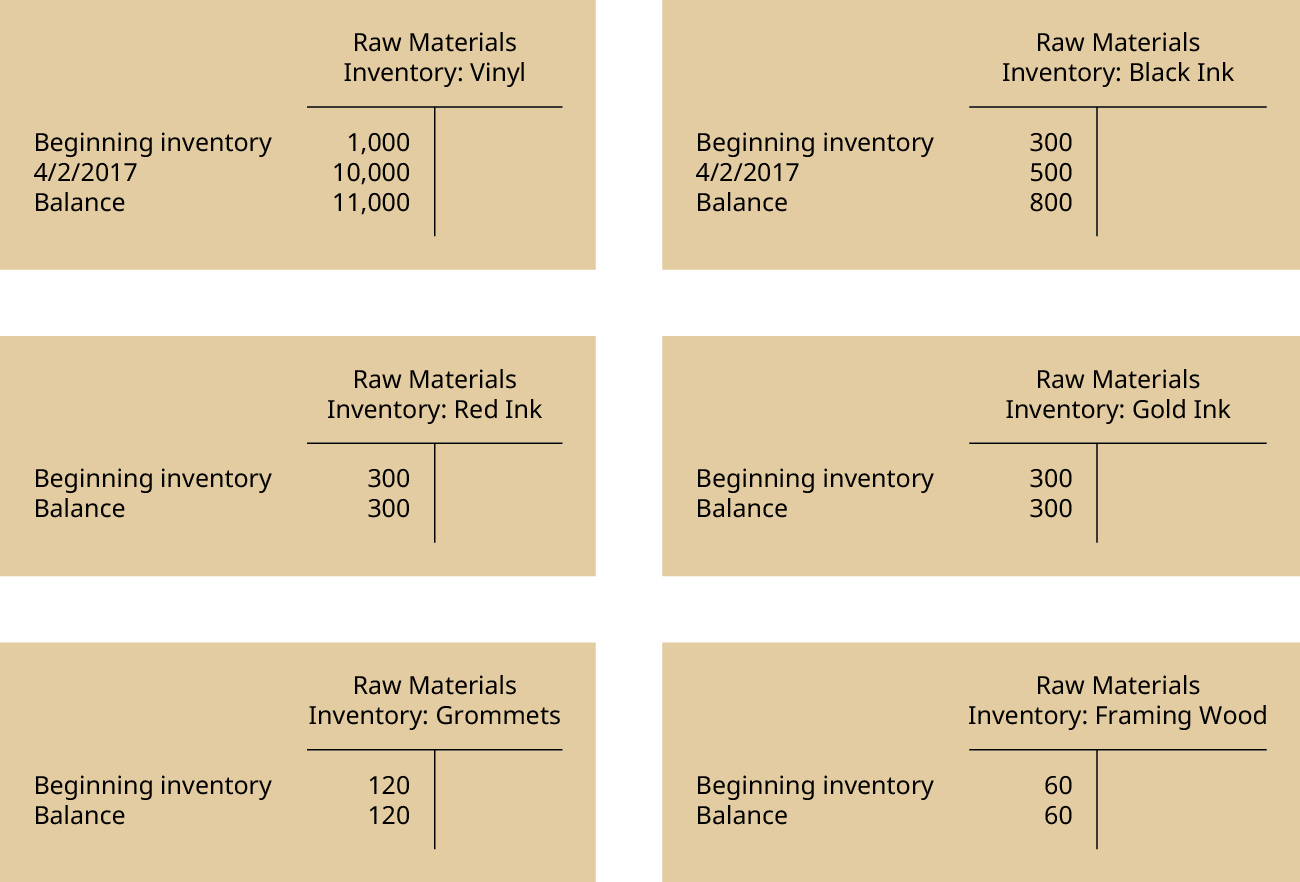
Traditional billboards with the design printed on vinyl include direct materials of vinyl and printing ink, plus the framing materials, which consist of wood and grommets. The typical billboard sign is 14 feet high by 48 feet wide, and Dinosaur Vinyl incurs a vinyl cost of $300 per billboard. The price for the ink varies by color. For this job, Dinosaur Vinyl needs two units of black ink at a cost of $50 each, one unit of red ink and one unit of gold ink at a cost of $60 each, twelve grommets at a cost of $10 each, and forty units of wood at a cost of $1.50 per unit. The total cost of direct materials is $700, as shown in Figure 8.19.
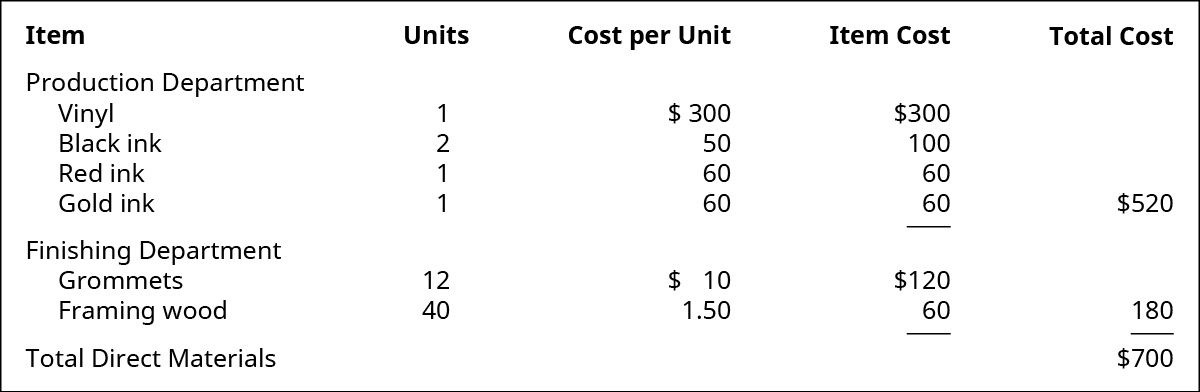
Some items are more difficult to measure per unit, such as adhesives and other materials not directly traceable to the final product. Their costs are assigned to the product as part of manufacturing overhead as indirect materials.
When Dinosaur Vinyl requests materials to complete Job MAC001, the materials are moved from raw materials inventory to work in process inventory. We will use the beginning inventory balances in the accounts that were provided earlier in the example. The requisition is recorded on the job cost sheet along with the cost of the materials transferred. The costs assigned to job MAC001 are $300 in vinyl, $100 in black ink, $60 in red ink, and $60 in gold ink. During the finishing stages, $120 in grommets and $60 in wood are requisitioned and put into work in process inventory. The costs are tracked from the materials requisition form to the work in process inventory and noted specifically as part of Job MAC001 on the preceding job order cost sheet. The movement of goods is illustrated in Figure 8.20.
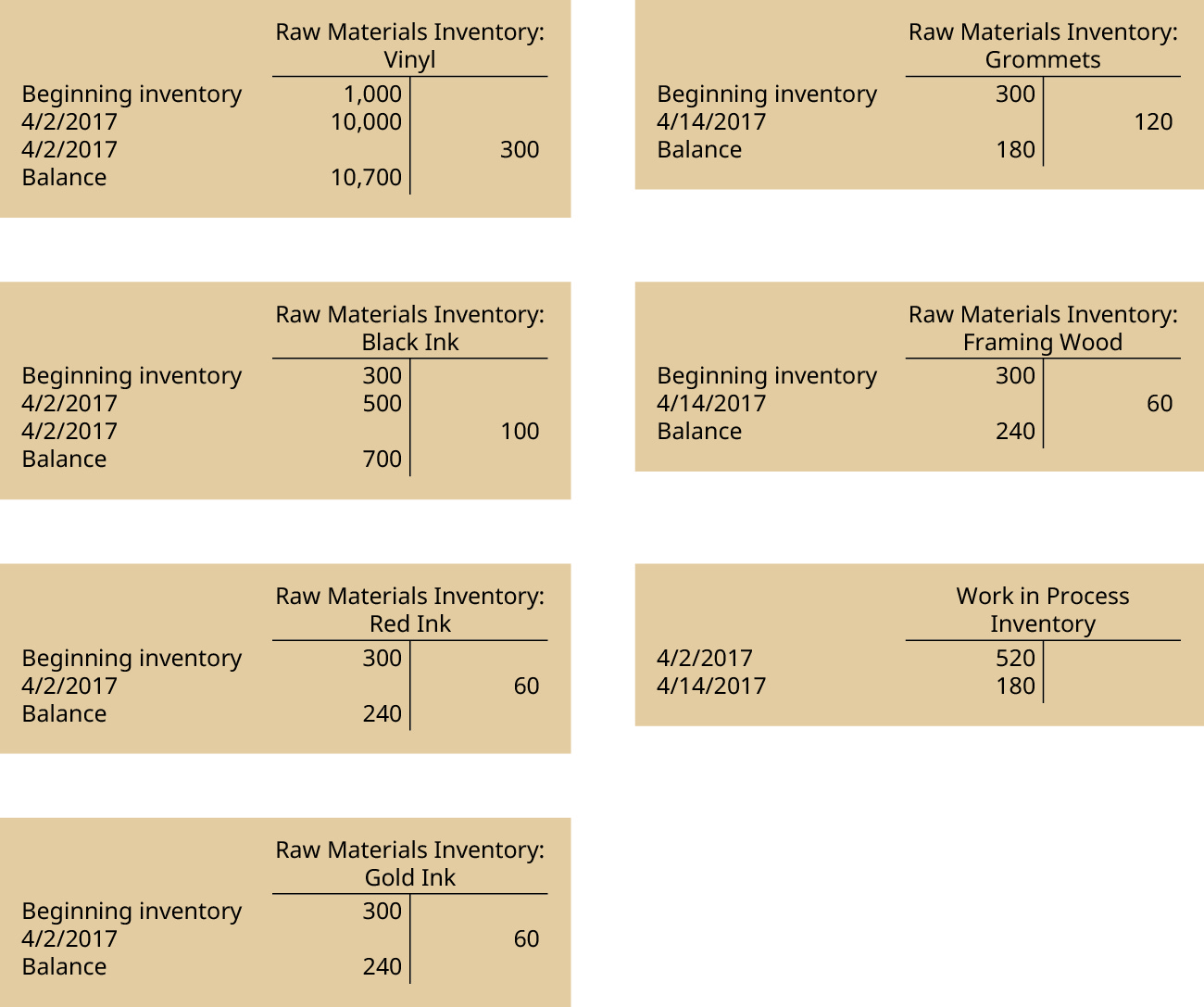
Each of the T-accounts traces the movement of the raw materials from inventory to work in process. The vinyl and ink were used first to print the billboard, and then the billboard went to the finishing department for the grommets and frame, which were moved to work in process after the vinyl and ink. The final T-account shows the total cost for the raw materials placed into work in process on April 2 (vinyl and ink) and on April 14 (grommets and wood).
Direct Labor
Direct labor is the total cost of wages, payroll taxes, payroll benefits, and similar expenses for the individuals who work directly on manufacturing a particular product. The direct labor costs for Dinosaur Vinyl to complete Job MAC001 occur in the production and finishing departments. In the production department, two individuals each work one hour at a rate of $15 per hour, including taxes and benefits. The finishing department’s direct labor involves two individuals working one hour each at a rate of $18 per hour. Figure 8.21 shows the direct labor costs for Job MAC001.
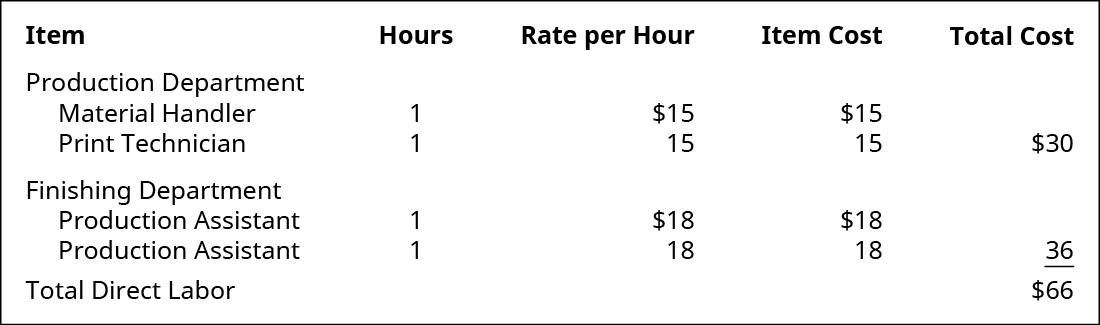
Job MAC001 is also manufactured with the work of individuals whose contributions cannot be directly traced to the product: These indirect labor costs are assigned to the product as part of manufacturing overhead.
A company can use various methods to trace employee wages to specific jobs. For example, employees may fill out time tickets that include job numbers and time per job, or workers may scan bar codes of specific jobs when they begin a job task. Figure 8.22 shows what time tickets might look like on Job MAC001. Please note that in the employee time tickets that are displayed, each employee worked on more than one job. However, we are only going to track the expenses for Job MAC001.
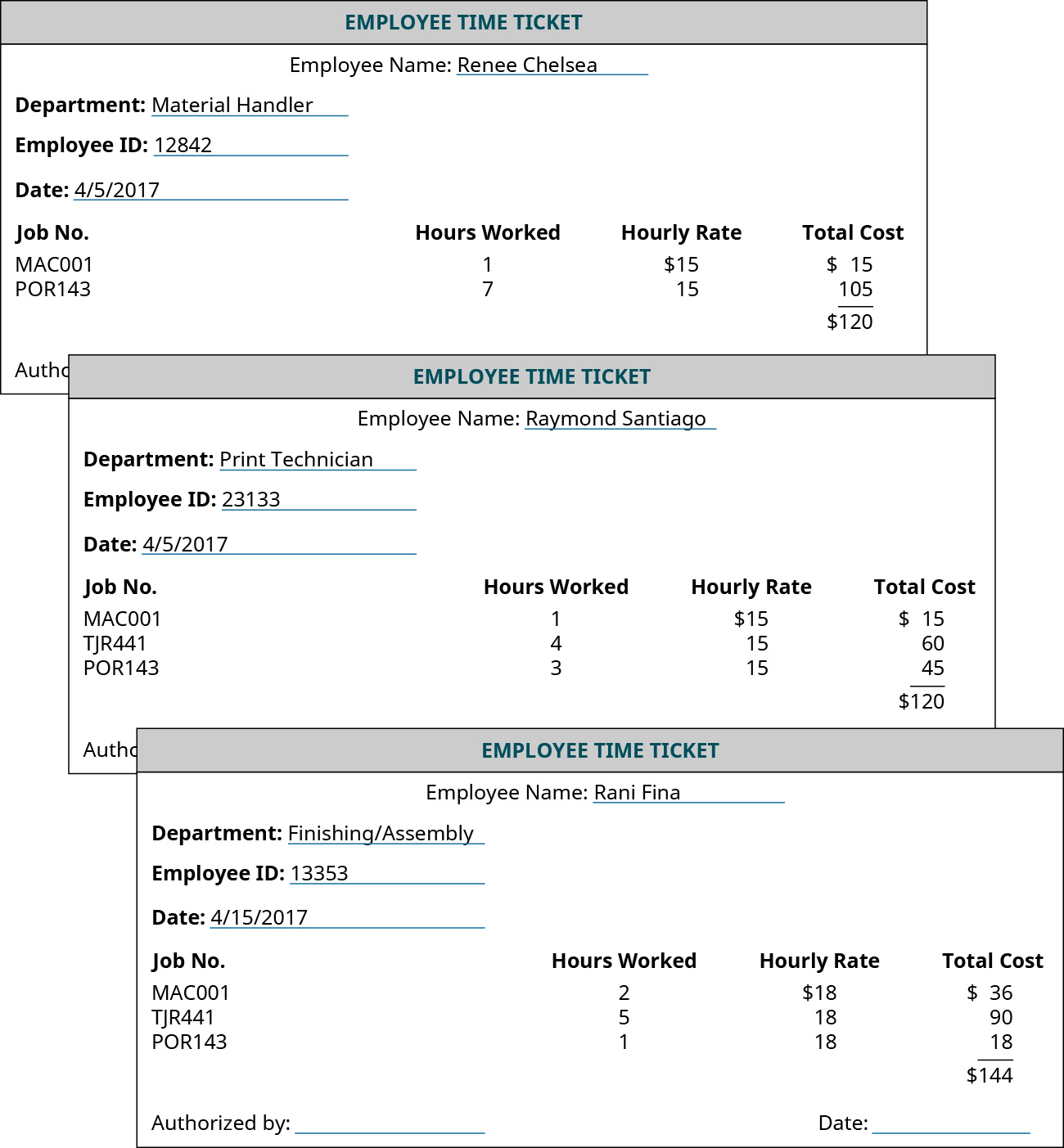
When the accounting department processes time tickets, the costs are assigned to the individual jobs, resulting in labor costs being recorded on the work in process inventory, as shown in Figure 8.23.
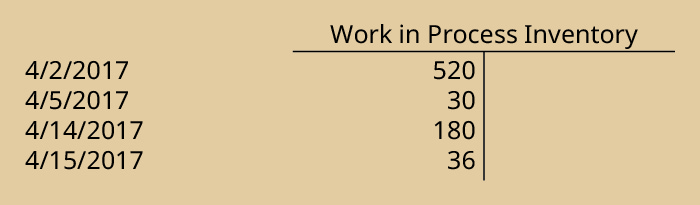
Manufacturing Overhead
Recall that the costs of a manufactured item are direct materials, direct labor, and manufacturing overhead. Costs that support production but are not direct materials or direct labor are considered overhead. Manufacturing overhead has three components: indirect materials, indirect labor, and overhead.
Indirect Materials
Indirect material costs are derived from the goods not directly traced to the finished product, like the sign adhesive in the Dinosaur Vinyl example. Tracking the exact amount of adhesive used would be difficult, time consuming, and expensive, so it makes more sense to classify this cost as an indirect material.
Indirect materials are materials used in production but not traced to specific products because the net informational value from the time and effort to trace the cost to each individual product produced is impossible or inefficient. For example, a furniture factory classifies the cost of glue, stain, and nails as indirect materials. Nails are often used in furniture production; however, one chair may need 15 nails, whereas another may need 18 nails. At a cost of less than one cent per nail, it is not worth keeping track of each nail per product. It is much more practical to track how many pounds of nails were used for the period and allocate this cost (along with other costs) to the overhead costs of the finished products.
Indirect Labor
Indirect labor represents the labor costs of those employees associated with the manufacturing process, but whose contributions are not directly traceable to the final product. These would include the costs of the factory floor supervisor, the factory housekeeping staff, and factory maintenance workers. For Dinosaur Vinyl, for example, labor costs for the technician who maintains the printers would be indirect labor. It would be too time consuming to determine how much of the technician’s time is attributable to each sign being produced. It makes much more sense to classify that labor expense as indirect labor.
It is important to understand that the allocation of costs may vary from company to company. What may be a direct labor cost for one company may be an indirect labor cost for another company or even for another department within the same company. Deciding whether the expense is direct or indirect depends on its task. If the employee’s work can be directly tied to the product, it is direct labor. If it is tied to the factory but not to the product, it is indirect labor. If it is tied to the marketing department, it is a sales and administrative expense, and not included in the cost of the product. For example, salaries of factory employees assembling parts are direct labor, salaries of factory employees performing maintenance are indirect labor, and salaries of employees in the marketing department are sales and administration expenses.
Overhead
The last category of manufacturing overhead is the overhead itself. These costs are necessary for production but not efficient to assign to individual product production. Examples of typical overhead costs are production facility electricity, warehouse rent, and depreciation of equipment.
But note that while production facility electricity costs are treated as overhead, the organization’s administrative facility electrical costs are not included as as overhead costs. Instead, they are treated as period costs, as office rent or insurance would be.
When both administrative and production activities occur in a common building, the production and period costs would be allocated in some predetermined manner. For example, if a 10,000 square foot building were physically allocated at 4,000 square feet for administrative purposes and 6,000 square feet for production, a company might allocate its annual $30,000 property tax expense on a 40% ÷ 60% basis, or $12,000 as a period cost for the administrative offices and a production (overhead) cost of $18,000.
Accounting for Manufacturing Overhead
In all costing systems, the expense recognition principle requires costs to be recorded in the period in which they are incurred. The costs are expensed when matched to the revenue with which they are associated; this is commonly referred to as having the expenses follow the revenues. This explains why raw material purchases are not assigned to the job until the materials are requested. When companies use an inventory account, the product costs are expensed when the inventory is sold. It is common to have an item produced in one year, such as 2017, and expensed as cost of goods sold in a later year, such as 2018. In addition to the previously mentioned revenue recognition treatment, this treatment is justified under GAAP’s matching principle. If the inventory has not been sold, the company has an inventory asset rather than an expense.
The expense recognition principle also applies to manufacturing overhead costs. The manufacturing overhead is an expense of production, even though the company is unable to trace the costs directly to each specific job. For example, the electricity needed to run production equipment typically is not easily traced to a particular product or job, yet it is still a cost of production. As a cost of production, the electricity—one type of manufacturing overhead—becomes a cost of the product and part of inventory costs until the product or job is sold. Fortunately, the accounting system keeps track of the manufacturing overhead, which is then applied to each individual job in the overhead allocation process.
Managers use the information in the manufacturing overhead account to estimate the overhead for the next fiscal period. This estimated overhead needs to be as close to the actual value as possible, so that the allocation of costs to individual products can be accurate and the sales price can be properly determined.
Properly allocating overhead to the individual jobs depends on finding a cost driver that provides a fair basis for the allocation. A cost driver is a production factor that causes a company to incur costs. An example would be a bakery that produces a line of apple pies that it markets to local restaurants. To make the pies requires that the bakery incur labor costs, so it is safe to say that pie production is a cost driver. It should also be safe to assume that the more pies made, the greater the number of labor hours experienced (also assuming that direct labor has not been replaced with a greater amount of automation). We assume, in this case, that one of the marketing advantages that the bakery advertises is 100% handmade pastries.
In traditional costing systems, the most common activities used as cost drivers are direct labor in dollars, direct labor in hours, or machine hours. Often in the production process, there is a correlation between an increase in the amount of direct labor used and an increase in the amount of manufacturing overhead incurred. If the company can demonstrate such a relationship, they then often allocate overhead based on a formula that reflects this relationship, such as the upcoming equation. In the case of the earlier bakery, the company could determine an overhead allocation amount based on each hour of direct labor or, in other cases, based on the ratio of anticipated total direct labor costs to total manufacturing overhead costs.
For example, assume that the company estimates total manufacturing overhead for the year to be $400,000 and the direct labor costs for the year to be $200,000. This relationship would lead to $2.00 of applied overhead for each $1.00 of direct labor incurred. The manufacturing overhead cost can be calculated and applied to each specific job, based on the direct labor costs. The formula that represents the overhead allocation relationship is shown, and it is the formula for overhead allocation:

For example, Dinosaur Vinyl determined that the direct labor cost is the appropriate driver to use when establishing an overhead rate. The estimated annual overhead cost for Dinosaur Vinyl is $250,000. The total direct labor cost is estimated to be $100,000, so the allocation rate is computed as shown:

Since the direct labor expense for MAC001 is $66, the overhead allocated is $66 times the overhead application rate of $2.50 per direct labor dollar, or $165, as shown:

Figure 8.27 shows the journal entry to record the overhead allocation.
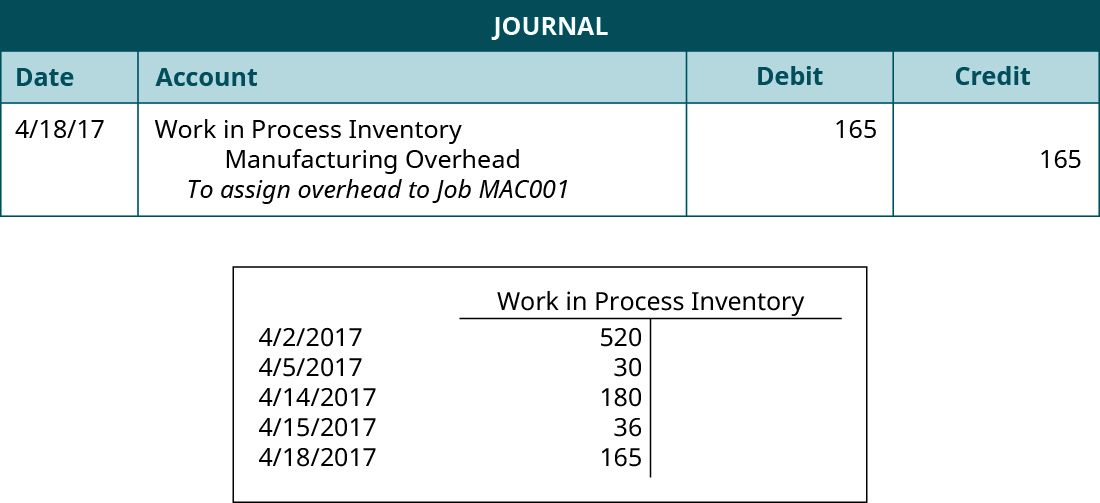
Long Descriptions
A T-account for Work In Process Inventory. Outside of the T-account is a label “Production costs” with arrows pointing to each of the components on the debit side of the T-account: “Direct Materials”, “Direct Labor”, and “Manufacturing Overhead.” The credit side of the T-account says “Transferred to Finished Goods Inventory” with an arrow pointing outside of the right side of the T account with the label “Finished goods inventory” Return
A Materials Requisition Form with the heading “Dinosaur Vinyl, Inc. The identifying lines are filled out: Materials requisition No. 3392, Job No.: MAC001, Date of Request: 4/5/2017, Date Needed: 4/5/2017. Below is a section with four columns labeled “Description”, “Quantity”, “Unit Cost”, and “Total Cost.” The rows say: “Raw materials inventory: Vinyl, 1, 300, 300; Raw materials inventory: Black ink, 2, 50, 100; Raw materials inventory: Red ink, 1, 60, 60; Raw materials inventory: Gold ink, 1, 60, 60; Raw materials inventory: Grommets, 12, 10, 120; Raw materials inventory: Framing wood, 40, 1.50, 60”. The Total Cost column shows “520.” Below are signatures for “Requested by” signed by John Ming and “Authorized by” signed by Isla Clark, both dated 4/5/17. Return
Six T-Accounts. The one headed “Raw Materials Inventory: Vinyl has three debit entries: Beginning inventory 1,000, 4/2/2017 10,000, Balance 11,000. The one headed Raw Materials Inventory: Black Ink has three debit entries: Beginning inventory 300, 4/2/2017 500, Balance 800. The one headed Raw Materials Inventory: Red Ink has two debit entries: Beginning inventory 300, Balance 300. The one headed Raw Materials Inventory: Gold Ink has two debit entries: Beginning inventory 300, Balance 300. The one headed Raw Materials Inventory: Grommets has two debit entries: Beginning inventory 120, Balance 120. The one headed Raw Materials Inventory: Framing Wood has two debit entries: Beginning inventory 60, Balance 60. Return
A five column chart showing the cost of the direct materials used. The headings are “Item”, “Units”, “Cost per Unit”, “Item Cost”, and “Total Cost.” The figures are divided by department. The Production Department rows are: Vinyl, 1,$300, $300; Black ink, 2, 50, 100; Red ink, 1, 60, 60; Gold ink, 1, 60, 60. The item cost is then totaled in the total cost column as $520. The Finishing Department rows are: Grommets, 12, $10, $120; and Framing Wood, 40, 1.50, 60. The item cost is then totaled in the total cost column as 180. The total cost for the two departments is then totaled as $700 for the Total Direct Materials. Return
Seven T-accounts: The one headed “Raw Materials Inventory: Vinyl” has two debit entries: Beginning inventory 1000, 4/2/2017 10,000, one credit entry: 4/2/2017 300, and a debit Balance of 300. The one headed “Raw Materials Inventory: Black Ink” has two debit entries: Beginning inventory 300, 4/2/2017 500, one credit entryside: 4/2/2017 100, and a debit Balance of 700. The one headed “Raw Materials Inventory: Red Ink” has a debit: Beginning inventory 300, one credit entry: 4/2/2017 60, and a debit Balance of 240. The one headed “Raw Materials Inventory: Gold Ink” has a debit: Beginning inventory 300, one credit: 4/2/2017 60, and a debit Balance of 240. The one headed “Raw Materials Inventory: Grommets” has a debit: Beginning inventory 300, one credit entry: 4/14/2017 120, and a debit Balance of 180. The one headed “Raw Materials Inventory: Wood” has a debit: Beginning inventory 300, two credit entries: “used in other jobs 200” and 4/14/2017 60, and a debit Balance of 40. The one headed “Work in Process Inventory” has two debit entries: 4/2/2017 520, and 4/14/2017 180. Return
A five column chart calculating the Direct Labor. The headings are: “Item”, “Hours”, “Rate per Hour”, “Item Cost”, and “Total Cost.” The figures are divided by department. The Production Department rows are: Material Handler, 1, $15, $15; Print Technician, 1, 15, 15. The item cost is then totaled in the total cost column as $30. The Finishing Department rows are: Production Assistant, 1, $18, $18; Production Assistant, 1, $18, $18. The item cost is then totaled in the total cost column as $36. The total cost for the two departments is then totaled as $66 for the Total Direct Labor. Return
Three forms labeled “Employee Time Ticket.” They each have a place to fill out the Employee Name, Department, Employee ID, and Date. Then there are four columns the form with headings: “Job No.”, “Hours Worked”, “Hourly Rate”, and “Total Cost”. The first ticket is Renee Chelsea, material handler, ID# 12842, 4/5/2017 with the following information: MAC001 1, 15, 15; POR143, 7,15,105. Her total cost is added to be 120. The second ticket is Raymond Santiago, Print Technician, ID#23133, 4/5/2017 with the following information: MAC001 1, 15, 15; TJR441 4, 15, 60, POR143, 3, 15, 45. His total is 120. The last ticket is Rani Fina, Finishing/Assembly, ID#13353, 4/15/2017 with the following information: MAC001, 2, 18, 36; TJR441 5, 18, 90; POR143, 1, 18, 18; for a total of 144. Each ticket has a place on the bottom to be authorized with a signature and a date. Return
A journal entry dated 4/18/17 lists Work in Process Inventory with a debit of 165, Manufacturing Overhead with a credit of 165, and the note “To assign overhead to Job MAC0001. A T-account for “Work in Process Inventory” with five debit entries: 4/2/2017 520, 4/5/2017 30, 4/10/2017 30, and 4/15/2017 36, 4/18/2017 165. Return